«За последние 3 месяца мы произвели больше аэрозолей, чем за весь 2021 год»
Интервью с руководителем производства расходных материалов «КЛЕВЕР» для ПВК и МПКОтечественные расходные материалы «КЛЕВЕР» для контроля проникающими веществами и магнитопорошковой дефектоскопии выпускаются усилиями трёх предприятий: научно-производственного центра «Кропус», лаборатории «ОМНИКОМ» и компании «Формула НК». И хотя это три разные организации, фактически проект родился и развивается по сей день благодаря усилиям большой команды экспертов из Москвы и Санкт-Петербурга, которая сложилась уже очень давно. Коммерческий директор компании «Формула НК» Лариса Сергеевна Хотулева рассказала редакции «Дефектоскопист.ру» о том, как создавалась линейка расходников «КЛЕВЕР», как себя чувствует производство в новой реальности, какие актуальные проблемы приходится решать и что нового ждёт российских дефектоскопистов МПД и ПВК.
Лариса Сергеевна, расскажите, пожалуйста, подробнее об участии специалистов «Формулы НК» в производстве расходных материалов «КЛЕВЕР» для капиллярной и магнитопорошковой дефектоскопии?
Расходные материалы «КЛЕВЕР» – это продукт совместной работы. Компания «ОМНИКОМ», чьи данные указаны на этикетке, занимается разработкой рецептур, производством, является держателем торговой марки и технических условий. Все 100% продукции ею производятся для компании «КРОПУС», в чьем ведении находятся коммерческие вопросы: ценовая политика, формирование склада, продвижение, работа с дилерами, розничные и оптовые продажи, а также планирование. Персонал «Формулы НК» с самого начала был задействован в качестве экспертов в магнитопорошковом и капиллярном контроле, а также в качестве партнера – производителя специального оборудования.
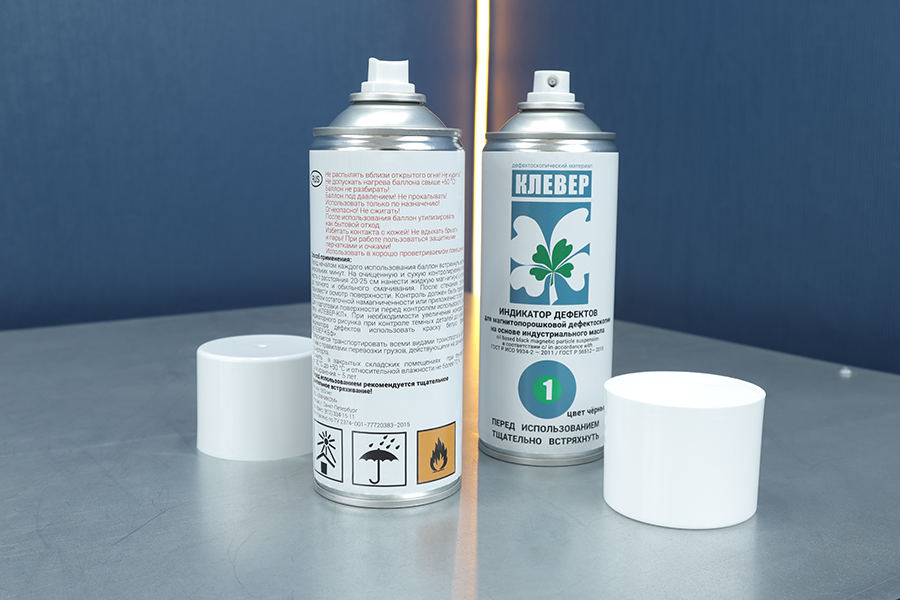
Принять решение «производить расходные материалы в аэрозольной упаковке» было довольно просто. Не простым был выбор пути, по которому мы пойдем.
Что мы видим сейчас на рынке? Расходные материалы иностранных производителей в оригинальной упаковке от официальных дилеров, расходные материалы иностранных производителей, упакованные в России и продаваемые под российской торговой маркой и расходные материалы российского производства.
Безусловно, масса преимуществ у частичной локализации производства: небольшие стартовые вложения, просчитываемая себестоимость, короткий период выхода на рынок с ШИРОКОЙ линейкой продуктов от самых простых до самых сложных. В краткосрочном периоде – это весьма заманчивая перспектива с очень небольшими, в основном микроэкономическими, рисками.
Если же посмотреть на частичную локализацию с точки зрения долгосрочной перспективы, то становятся очевидны макроэкономические риски, к коим, в частности, относятся и геополитические.
В долгосрочной перспективе самый большой риск – это риск НЕОБЛАДАНИЯ ОСНОВНОЙ ТЕХНОЛОГИЕЙ изготовления продукта. Лишиться по тем или иным причинам основного иностранного партнера-поставщика автоматически означает лишиться конечного продукта, а возможно, и бизнеса.
Отчасти по этим причинам мы приняли решение организовать производство с нуля. Есть, конечно, еще эмоциональные причины, но опираться в бизнесе целиком на них – иррационально.
Определение стратегии – это был первый сложный этап.
Следующие сложности, с которыми мы столкнулись, случились в процессе бета-тестинга, во время которого мы бесплатно раздавали аэрозоли «КЛЕВЕР», ожидая взамен отзыв о продукте.
В общей сложности мы раздали более 5 тысяч аэрозольных баллонов. Лишь от трети респондентов (назовем их маркетинговым термином) мы получили хоть какой-то ответ. При этом из всех полученных отзывов лишь 4,5% были пригодны для дальнейшего анализа, т.е. содержали описание объекта контроля, на котором тестировались расходные материалы, условий и процедуры проведения контроля, а также содержали фото промежуточных и финальных результатов с указанием, почему эти результаты удовлетворяют / не удовлетворяют. И несмотря на то, что положительные отзывы превалировали над отрицательными, шумиха, развернувшаяся на форуме вокруг наших аэрозолей, напоминала атаку.
Нам вменяли в вину все: от запаха пенетранта до совпадения по цветам этикеток двух из трех аэрозолей в составе комплекта для капиллярного контроля. Поверьте, запах присущ не только нашим аэрозолям. ВСЕМ! Но есть более или менее эффективные подавители запаха, которые никак не устраняют вредные вещества из воздуха во время контроля, а только МАСКИРУЮТ их наличие для человека. Именно поэтому есть требование к обеспечению минимум трехкратного воздухообмена в помещениях, где проводится капиллярный контроль. Что касается якобы похожего дизайна упаковки, то просто для сравнения приводим фото нашего комплекта до смены цвета этикетки и после, а также фото аэрозольных баллонов наших конкурентов. Как говорится, без комментариев.
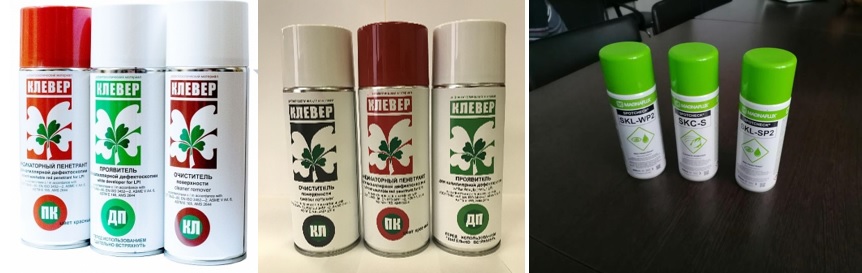
Этот этап был очень сложным. Скорее морально. Но мы продолжаем работать, делать новое, улучшать уже сделанное, решаем проблемы, которые возникали и возникают постоянно. Очень выручает поддержка друг друга: есть ряд компаний на рынке, связанные не только деловыми, но и дружескими отношениями. Это помогает в трудных ситуациях.
И сейчас мы переживаем очередной непростой этап.
К слову о непростом этапе. Насколько Ваши производственные мощности оказались готовы к росту объёмов выпускаемой продукции за последнее время? И ожидаете ли Вы перераспределения долей рынка расходников для ПВК и МПД?
Нам сейчас не просто: основная проблема последних месяцев – адаптация к взрывному спросу. За 3 месяца с февраля по май 2022 года мы произвели аэрозолей больше, чем за весь 2021 год. Конечно, такое сложно было прогнозировать. И если наших производственных мощностей более, чем достаточно для удовлетворения возросшего спроса, то человеческих ресурсов порой не хватает. Это другая логистика, другие объемы закупок, другая, более интенсивная, работа с поставщиками сырья, материалов и услуг, которые сейчас испытывают те же трудности, что и мы. Однако мы очень стараемся.
Можно ли ожидать перераспределения рынка? Сложный вопрос. В первую очередь из-за укрепления рубля, в связи с которым себестоимость импорта даже с учетом подорожавшей и «кривой» логистики становится сопоставима с нашей производственной себестоимостью. Нам бы все-таки хотелось уповать на лояльность российских заказчиков к российским производителям, это позволило нам хотя бы не лишиться тех новых клиентов, которые ранее не использовали «КЛЕВЕР», но сейчас из-за отсутствия аэрозолей других производителей попробовали и не разочаровались. Мы не собираемся злоупотреблять хорошим отношением, но без него у нас нет шансов быстро развиваться: дорабатывать уже существующие рецептуры, расширять ассортимент, делать какие-то специальные составы, обновлять оборудование, следить за качеством и иметь складской запас готовой продукции и т.д. Крайне сложно за 5 лет преодолеть тот путь, по которому наши иностранные конкуренты начали идти еще в прошлом веке во время Второй мировой войны. При этом требования к нам предъявляются одинаковые, и мы, несмотря ни на что, стараемся им соответствовать.
Что из сырья и упаковочных материалов Вы делаете своими силами, а что закупаете у поставщиков? Все ли они базируются в РФ?
Более 70% сырья и материалов мы закупали в России. Как и у «Формулы НК», одним из ключевых принципов производственной стратегии компании «ОМНИКОМ» было и есть предпочтительное отношение к российским производителям. В первую очередь мы всегда проверяем, что есть у отечественных предприятий. Если не находим нужного материала, но видим потенциал и возможность для дальнейшей работы, то совместно с производителем пытаемся «допилить» качество или свойства материала до нужных нам. Параллельно, конечно, приходилось закупать материал заграницей: в Китае и Индии. Да, работа с отечественными производителями велась довольно медленно, по остаточному принципу, но сейчас, когда ее подхлестнули санкции, мы, по крайней мере, стартуем не с нуля.
Можете рассказать о том, где находится, каким оборудованием сегодня оснащено производство материалов «КЛЕВЕР»?
Производство расходных материалов «КЛЕВЕР» началось с лаборатории, организованной в маленьком городе в Кировской области, известном своим огромным химическим комбинатом. Лабораторию мы оснастили, откровенно говоря, довольно старым оборудованием, и главная ее ценность состояла (и состоит) в людях, которые в ней работают. Они – настоящие профессионалы «старой школы». В этой лаборатории разрабатывались и дорабатывались рецептуры всех составов «КЛЕВЕР», которые производит компания «ОМНИКОМ». Работа здесь ведется и в настоящее время, однако на данный момент «ОМНИКОМ» переносит лабораторию в Санкт-Петербург. Причин несколько:
- увеличившиеся объемы технологического надзора в связи с увеличением объема производства. Если ранее химик-технолог выезжал на производство в лучшем случае раз в квартал, то теперь есть необходимость в его постоянном присутствии.
- увеличившиеся объемы разработок.
- давно назревшая модернизация. Нами закуплено все основное необходимое лабораторное оборудование. Современное, удобное и эффективное.
Само производство, то есть технологическое оборудование для воспроизведения всех рецептур в промышленных объемах, находится в Санкт-Петербурге.
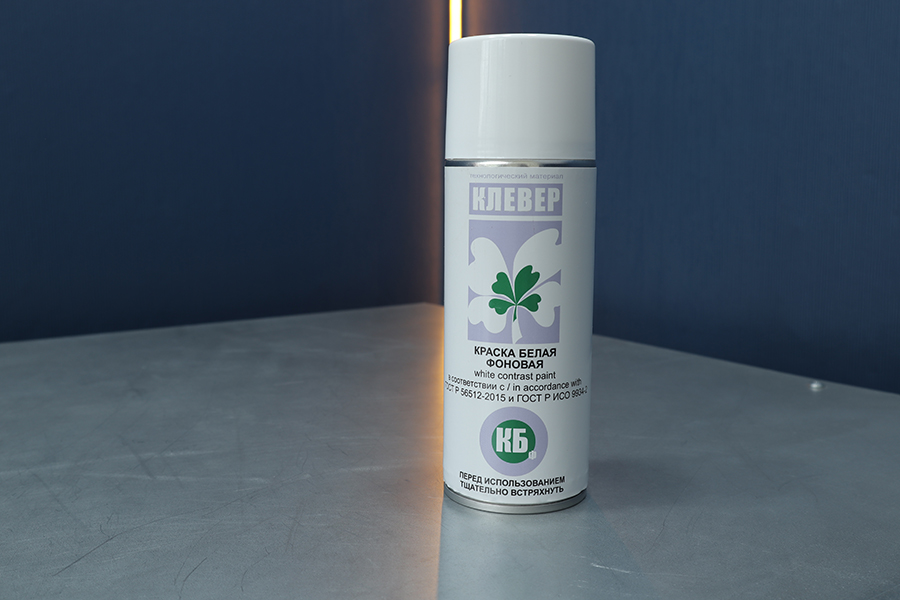
Нет, мы не видим больших рисков. Мы используем или очень простое оборудование, или оборудование собственного производства. В миксере для производства пенетранта даже контроллер российский. Лабораторное оборудование, закупленное в 1 квартале 2022 года, хоть и импортное отчасти, но оно, во-первых, новое, во-вторых, старое оборудование мы собираемся консервировать, чтобы при необходимости иметь возможность использовать его на замену.
Какие технологические процессы самые сложные в производстве пенетрантов и магнитных суспензий?
Если не учитывать разработку рецептур, то самый сложный производственный процесс на данный момент – это изготовление пенетранта. Для него потребовалось спроектировать и сделать специальный миксер, на форуме была об этом информация.
Что самое сложное для дефектоскопистов (контролёров ОТК), выполняющих ПВК и МПД, в переходе с расходников одной марки на материалы другого бренда? Какие здесь могут быть технические, нормативные, ментальные препятствия?
Предположим, вы любите сырники. По вашему мнению, ваша мама великолепно их готовит. Вам все нравится: и как они выглядят, и как пахнут, и какие они на вкус. Потом вы переезжаете в другой город и приходите на завтрак в кафе. Вам приносят сырники. Они приготовлены по другому рецепту, немножко по-другому пахнут, немножко по-другому выглядят, немного другие на вкус, но тоже очень вкусные. Вы привыкли к маминым и сравниваете эти сырники с теми. Дальше все зависит от человека: один признает, что сырники из кафе ТОЖЕ вкусные, хоть и немного отличные от тех, к которым он привык; а другой будет кривиться и настаивать на том, что все прочие сырники в мире не сырники, потому что единственно правильные сырники готовит его мама. Надеюсь, аналогия понятно =)
Если расходные материалы решают основную поставленную задачу – надежно выявляют требуемые дефекты, то остальное во многом – это субъективный фактор. Мы, как производитель, не можем скидывать со счетов то, какие требования (пусть даже субъективные) предъявляют к расходным материалам потребители, однако, мы не можем угодить каждому. Как с сырниками =)
Тогда спрошу про аппетит, который, как известно, приходит во время еды =) Понятное дело, сейчас очень сложно что-то планировать, но всё же: какие задачи Вы перед с собой ставите в среднесрочной перспективе? Какие новые проекты планируете реализовывать? Как будет развиваться производство материалов «КЛЕВЕР»? Можно ли что-то прогнозировать по изменению цен на продукцию?
Планировать сложно, но это необходимо. В ближайших планах ввести в полноценную эксплуатацию новую химлабораторию.
Кроме того, нами определены наиболее критичные позиции по сырью, используемому в наших рецептурах, здесь мы работаем по двум направлениям: над поддержанием складского запаса и над доработкой отечественных заместителей импортных компонентов для обеспечения бесперебойных поставок сырья.
Мы произвели пробную партию расходных материалов в крупной таре (жестяные канистры и бочки, пластиковая тара). Сейчас смотрим на спрос и думаем над организацией полноценной линии розлива для снижения доли ручного труда, уменьшения потерь при фасовке и более точного дозирования.
Кроме того, мы разрабатываем рецептуры и технологию изготовления концентратов магнитопорошковых суспензий с тем качеством, которое бы устроило специалистов «Формулы НК» (они самые придирчивые в отношении этого продукта) и могло соперничать с иностранными аналогами.
Безусловно и само собой разумеется – дальнейшая работа над повышением качества уже имеющихся продуктов и выпуск новых.
Благодарим за содержательные ответы. Ранее, напомним, на «Дефектоскопист.ру» были опубликованы результаты сравнительных испытаний источника УФ-освещения БРИЗ-УФ365 с импортными конкурентами (это тоже один из продуктов «Формулы НК»), отзыв о нём от АО «Силовые машины», а также видео-демонстрация типового алгоритма проверки работоспособности магнитопорошкового дефектоскопа на примере мобильного генератора тока «Балтиец 1000 АС» и стенда МД-300.