Метод акустической эмиссии для контроля трубопроводов
Метод акустической эмиссии (АЭ) широко практикуется на технологических и магистральных трубопроводах, в частности, на газопроводах, нефтепроводах, трубопроводах пара, горячей воды и пр. Это интегральный метод неразрушающего контроля (НК), позволяющий обследовать протяжённые участки трубопроводов целиком, даже если они по большей части скрыты под землёй или покрыты изоляцией. Технология основана на регистрации упругих колебаний – эмиссии волн напряжения, возникающих в металле вследствие структурных изменений: напряжённо-деформированного состояния, пластической деформации, внешних механических воздействий, образования трещин или иных дефектов и пр. Всё это сопровождается разрушением в кристаллах или скоплениях кристаллов, движением нарушенной кристаллической структуры (дислокацией) и образованием микро- и макротрещин. Акустико-эмиссионный контроль способен дать информацию о зарождении и развитии выше перечисленных дефектов, что помогает делать обоснованные выводы о реальном техническом состоянии трубопровода. Метод акустической эмиссии активно применяется аттестованными лабораториями неразрушающего контроля (ЛНК) и специалистами АЭ на трубопроводах - опасных производственных объектах (ОПО), подведомственных Федеральной службе по экологическому, технологическому и атомному надзору (Ростехнадзору). Особенно на этапе их эксплуатации, технического диагностирования (ТД), технического освидетельствования (ТО), экспертизы промышленной безопасности (ЭПБ).Содержание:
Как это работаетОграничения метода акустической эмиссии
Аппаратура
Технология контроля
Обработка сигналов
Где купить аппаратуру для акустико-эмиссионного контроля
Возможности применения метода акустической эмиссии для контроля трубопроводов
Метод акустической эмиссии предполагает проведение контроля сварных соединений и основного металла трубопроводов непосредственно в процессе эксплуатации либо параллельно с испытаниями – гидравлическими или, реже, пневматическими. АЭ-контроль может проводиться по достижении срока, предписанного отраслевыми стандартами, конструкторской либо эксплуатационной документацией, а также по истечении нормативного срока службы объекта, либо вследствие его преждевременного выхода из строя, аварийной ситуации и пр.Локальная перестройка структура материала и местные разрушения возникают на магистральных трубопроводах в результате:
- развития технологических дефектов и дефектов монтажа с образованием зон перенапряжения;
- интенсивных пластических деформаций и хрупко-пластического разрушения, в частности – двойникования (поворота определённой части кристаллической решётки на некоторый угол относительно остального объёма кристалла) и зернограничного скольжения;
- подвижек грунта;
- коррозионных повреждений (в частности, межкристаллитной коррозии);
- температурных воздействий, статистических и динамических нагрузок и пр.
- фазовые превращения и переход металла в пластическое состояние;
- процесс развития трещин, расслоений, закатов, непроваров, свищей, прожогов, пор, кратеров и прочих дефектов основного металла и сварных соединений. В частности, это может быть трение «берегов» трещин и разрушение продуктов коррозии в их полости;
- утечки через сквозные дефекты либо разуплотненную запорную арматуру, заглушки и фланцевые соединения и связанные с этим гидродинамические и аэродинамические явления;
- разрушение шлаковых включений;
- разрушение продуктов электрохимической коррозии, коррозионное растрескивание и пр.
Применительно к технологическим и магистральным трубопроводам метод акустической эмиссии привлекателен также другими достоинствами.
- Техническая диагностика трубопровода без вывода из эксплуатации. Текущие эксплуатационные параметры транспортировки и хранения среды зачастую могут даже оказаться достаточными для проведения акустико-эмиссионного контроля.
- Сравнительно простая и недорогая подготовка поверхности трубопровода. Метод акустической эмиссии в ряде случаев является безальтернативным решением для диагностирования трубопроводов, недоступных для контроля в полном объёме иными методами. Например, когда речь идёт о подземных трубопроводах, а также наземных на большой высоте, в обмуровке, под изоляционным покрытием. АЭ-контроль позволяет обследовать даже те участки, которые проходят в технологических каналах или расположены вплотную к стенам зданий и сооружений либо к другим препятствиям. Для установки преобразователей акустической эмиссии (ПАЭ) требуется подготовка лишь отдельных небольших площадок на верхней образующей трубопровода. Если он находится под землёй, то для этого не нужно его полностью откапывать – достаточно сделать несколько шурфов. В зависимости от марки сплава, толщины металла, используемой аппаратуры (ПАЭ, усилители, центральный блок) – акустико-эмиссионный метод позволяет за один "подход" обследовать участки протяжённостью до 100 м. И поскольку датчики в процессе обследования остаются неподвижными – никакого сканирования не предполагается, а потому шероховатость и волнистость поверхности оказывают меньше влияния на результаты, чем, например, в ультразвуковой дефектоскопии.
- Высокая чувствительность к развивающимся дефектам, хорошая выявляемость трещин, течей и т.д. Повреждения трубопровода могут быть выявлены на самых ранних стадиях, задолго до критических разрушений. В реальных производственных условиях на трубопроводах метод акустической эмиссии способен обнаруживать приращение трещин всего в несколько долей мм. Предельную чувствительность акустико-эмиссионной аппаратуры, по теоретическим расчётам, оценивают и вовсе в 1x0,000001 кв. мм, что эквивалентно скачку трещины протяжённостью всего 1 мкм на тот же 1 мкм. При этом положение и пространственная ориентация объекта фактически никак не влияет на выявляемость дефектов. В отличие, например, от магнитопорошковой дефектоскопии, где важно следить за позиционированием объектов относительно намагничивающего устройства и учитывать угол между предполагаемой ориентацией поверхностных несплошностей и направлением магнитных силовых линий. Для метода акустической эмиссии всё это не имеет никакого значения.
- Возможность организации непрерывного мониторинга для наиболее оперативного обнаружения активных концентраторов напряжения. Акустико-эмиссионный контроль даёт информацию о техническом состоянии трубопровода в режиме реального времени. Поэтому одно из важнейших условий при проведении АЭ-контроля – связь с другим эксплуатационным персоналом, ответственным за нагружение объекта, например, за гидравлические или пневматические испытания. У специалистов АЭ должна быть возможность оперативно связаться с работниками, которые осуществляют изменение нагрузки, чтобы при угрозе возникновения критических разрушений в срочном порядке остановить испытания или изменить параметры нагружения. Аналогично это работает и при организации непрерывного мониторинга опасных производственных объектов. АЭ-метод неразрушающего контроля позволяет оперативно реагировать на образование локальных повреждений и тем самым не доводить ситуацию до катастрофических последствий.
- Безопасность для персонала. Здесь нет ионизирующего излучения, как в радиографическом контроле, например. Метод акустической эмиссии предполагает размещение операторов на некотором отдалении от трубопровода, в отдельном отапливаемом помещении либо в передвижной лаборатории на базе фургона, грузовика или прицепа.
Контроль трубопроводов методом акустической эмиссии выполняют аттестованные лаборатории и аттестованные специалисты I, II и III уровня. Чаще всего в руководящих документах и технических заданиях содержится требование о том, чтобы АЭ-контроль проводился бригадой, состоящей из не менее чем двух специалистов. Как минимум, один из них должен иметь II или III квалификационный уровень. По состоянию на декабрь 2022 года, аттестация специалистов АЭ чаще всего проводится по СДАНК-02-2020 «Правила аттестации персонала в области неразрушающего контроля» либо по СНК ОПО РОНКТД-02-2021 «Система неразрушающего контроля на опасных производственных объектах. Аттестация специалистов неразрушающего контроля». Первый документ действует в рамках Единой системы оценки соответствия в области промышленной безопасности, экологической безопасности, безопасности в энергетике и строительстве с координирующим органом НТЦ «Промышленная безопасность. Второй документ относится к Системе неразрушающего контроля на опасных производственных объектах, созданной под эгидой Российского общества по неразрушающему контролю и технической диагностике (РОНКТД) и СРО «Ассоциация «НАКС». Оба этих документа мы подробно сравнивали здесь. По каким именно правилам должны подтвердить квалификацию специалисты для получения допуска к проведению акустико-эмиссионного контроля – определяется требованиями заказчика и отображается в договоре. Это может быть не только аттестация в указанных системах, но и, например, сертификация по ГОСТ Р ИСО 9712-2019 для лабораторий, аккредитованных в Национальной системе аккредитации. Наконец, помимо отечественных систем, в РФ распространена сертификация персонала НК и АЭ в частности по международным стандартам – ISO 9712:2021, SNT-TC-1A (ASNT) и др.
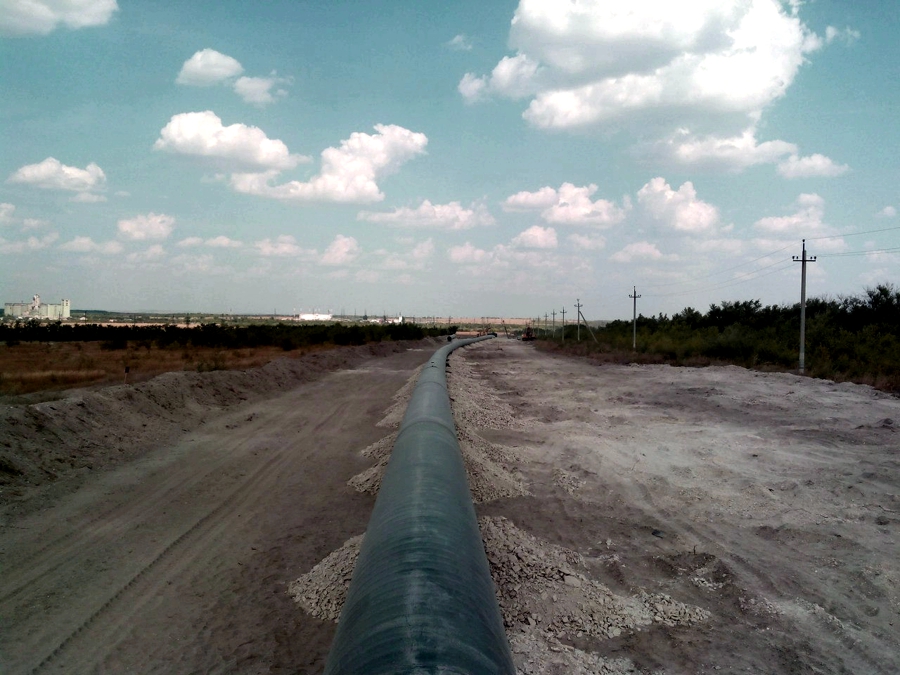
Проблемы применения метода акустической эмиссии по выявлению дефектов трубопроводов
При всех своих преимуществах, о которых было сказано выше, данный метод неразрушающего контроля связан с определёнными трудностями и ограничениями.- Необходимость нагружения объекта – для создания напряжённого состояния. На трубопроводах, особенно магистральных, большого диаметра, это может быть проблематично и затратно.
- Невысокая помехоустойчивость. Поскольку возникновение сигналов АЭ – это само по себе случайный импульсный процесс, то их легко спутать с шумами. «Полезные» сигналы могут иметь небольшую амплитуду, которая, правда, возрастает вместе с частотой по мере развития дефекта.
- Отсутствие чётких практических и методических обоснований для определения расстояния между преобразователями акустической эмиссии. Это зависит от скорости распространения звука, коэффициента затухания, зернистой структуры металла, диаметра, изоляции, качества аппаратуры – датчиков, блоков обработки информации и пр. В каких-то случаях расстояние до самого дальнего ПАЭ, с которого поступают стабильные сигналы, может достигать 45–60 м. При благоприятном стечении обстоятельств эта дистанция может достигать 80–100 м.
- Сложность и субъективность метода. В акустико-эмиссионном контроле фактически отсутствуют единые количественные критерии оценки степени опасности разрушений. В руководящих нормативно-технических документах есть лишь обобщённые положения рекомендательного характера. Поэтому, чтобы учесть все особенности объекта и верно трактовать сигналы акустической эмиссии, для каждого объекта составляют свою методику. И хотя современное программное обеспечение АЭ-контроля много чего умеет делать в автоматическом режиме – определяющую роль в настройке аппаратуры и расшифровке результатов всё равно играет квалификация специалистов.
- Необходимость привлечения дополнительных видов (методов) дефектоскопии для большей информативности при проведении технического диагностирования или экспертизы промышленной безопасности. Метод акустической эмиссии эффективен для выявления дефектов, развивающихся под нагрузкой, но фактически даёт мало представлений об их размерах, а также об остаточной толщине стенки трубопровода. Для получения этих сведений проводят дополнительный дефектоскопический контроль методами ВИК, УЗК, РК, ПВК, МК и др.
Практикуется и другой подход, когда, наоборот, выявленные благодаря другим видам НК недопустимые дефекты проверяют акустико-эмиссионным методом. И именно по результатам АЭ-контроля принимают решение о дальнейшей эксплуатации объекта.
Аппаратура для акустико-эмиссионного контроля трубопроводов
В общем случае используются следующие технические средства.- Преобразователи акустической эмиссии. Это первичные регистрирующие устройства, от которых зависит чувствительность контроля и рабочая частота. Последняя подбирается, в частности, с учётом шумов и затухания в материале объекта. Для технологических трубопроводов, например, обычно применяются преобразователи акустической эмиссии в низком диапазоне частот, от 20 до 60 кГц. Для металлов с большим затуханием (например, аустенитных сталей) используются частоты от 10 до 40 кГц, причём дополнительно к низкочастотным каналам используют высокие частоты. Датчики проходят обязательную калибровку. Она выполняется, как минимум, раз в год. Делается это в аккредитованных метрологических службах с использованием так называемых эталонных преобразователей акустической эмиссии. Также к ПАЭ прилагается паспорт с указанием их ключевых параметров, определённых по специальным методикам. Для акустико-эмиссионного контроля применяются резонансные преобразователи. Одно из главных к ним требований – стабильность рабочих характеристик во всём диапазоне температур, при которых проводится АЭ-контроль. Другое важное требование – помехозащищённость. Для закрепления преобразователей на поверхности трубопровода используются механические приспособления, магнитные держатели, армированный скотч, резиновые жгуты или клей. ПАЭ закрепляют непосредственно на трубе либо волноводе, с обязательным предварительным нанесением контактной жидкости – машинного масла, глицерина, геля, эпоксидной смолы без отвердителя или др.
- Предусилитель сигналов акустической эмиссии. Его располагают в непосредственной близости от преобразователя. Длина сигнального кабеля между ним и предусилителем не должна превышать 2 м. Предусилитель уже подключают к центральному блоку, допустимая длина сигнального кабеля – до 150 м. Коэффициент предварительного усилителя должен составлять от 20 до 60 дБ. Выбросы собственных помех в каналах должны быть минимальными. Для борьбы с искажениями передачи сигналов применяются селективные фильтры, математическая обработка средствами программного обеспечения и прочие решения.
- Центральный блок. Каждый канал соединён со своим датчиком. Именно центральный блок осуществляет регистрацию сигналов АЭ и производит их обработку для определения координат дефектов, оценки по нормам отбраковки и пр. Для поддержания производительности такие системы строят на базе быстродействующих промышленных компьютерах. Диагностические акустико-эмиссионные комплексы должны быть внесены в Государственный реестр средств измерений. Система должна производить обработку данных, перечисленных ниже, в режиме реального времени, выводить графическую информацию на периферийные устройства (монитор) и обеспечивать документирование результатов контроля. Акустико-эмиссионные комплексы работают в диапазоне частот не менее 10–500 кГц. Неравномерная амплитудно-частотной характеристики не должна превышать ±3 дБ. Такой же должна быть точность выравнивания чувствительности. Дополнительно к предварительному усилителю, о котором сказано выше, в центральном блоке предусматривается основной усилитель с коэффициентом усиления от 0 до 40 дБ и ступенчатой регулировкой с шагом 1 дБ.
- Программное обеспечение (ПО) для обработки данных. Современный софт позволяет управлять набором регистрируемых данных, вести журнал событий, осуществлять спектральный анализ сигналов акустической эмиссии и разделять его на частотные составляющие. Входящие данные обрабатываются по критериям, которые задаются оператором в соответствии с методикой и технологической картой. Визуализация источников импульсов АЭ на изображении (эскизе) трубопровода делает процесс контроля более наглядным.
Порядок проведения акустико-эмиссионного контроля трубопровода
Подготовка к АЭ-контролю начинается с изучения трубопровода, его проектной и технической документации, фактических условий и режимов эксплуатации. К наиболее важным сведениям, например, относятся:- дата строительства (монтажа) и ввода в эксплуатацию;
- диаметр, толщина стенки, марка сплава, его акустические свойства – скорость ультразвуковых волн, коэффициент затухания, характеристический импеданс и другие;
- информация о проведённых ранее ремонтах и диагностических обследованиях;
- рабочая среда и её температура;
- местоположение сварных соединений и пр.
Непосредственно на объекте его осматривают на предмет наличия конструктивных элементов, которые могут стать источником посторонних акустических шумов. Это может быть стук, шум от трения, утечки, проезжающий мимо транспорт и пр. По возможности предпринимают меры для того, чтобы уменьшить уровень шума. Сварочно-монтажные, строительные и другие работы на объекте и прилегающей территории (порядка 30 м), которые могут привести к появлению шумов, приостанавливают. Заглушки, необходимые для герметизации и последующего нагружения трубопровода, также предоставляются и монтируются заказчиком. Таким образом, метод АЭ предполагает тесное взаимодействие лаборатории с заказчиком и другими подрядчиками на объекте.
Преобразователи акустической эмиссии закрепляют на поверхности трубопровода. Её предварительно очищают от краски, защитной изоляции, льда и снега. В месте установки ПАЭ нужно обеспечить шероховатость не хуже Rz=40 мкм. Количество датчиков АЭ и шаг между ними рассчитывается индивидуально и определяется многими факторами, прежде всего – скоростью распространения акустических колебаний, реальным затуханием в материале, а также предписаниями методики проведения акустико-эмиссионного контроля и технологической карты. При необходимости, силами заказчика сооружаются леса и задействуются подъёмные механизмы для безопасной установки преобразователей акустической эмиссии. Для этого, опять же, силами заказчика, также выполняется зачистка поверхности.
После закрепления на трубопроводе преобразователи акустической эмиссии проверяют на работоспособность. Для этого применяются так называемые имитаторы АЭ – пьезоэлектрический преобразователь либо имитатор Су-Нельсона. Последний представляет собой карандаш с ломающимся графитовым стержнем диаметром 0,3–0,5 мм. Излом такого стержня, выдвинутого примерно на 2,5 мм и наклонённого на 30 градусов относительно поверхности трубопровода, имитирует сигнал АЭ и тем самым помогает определить реальное затухание в материале. Для работы с пьезоэлектрическим преобразователем-имитатором нужен генератор с частотой возбуждения импульсов от 1 до 100 Гц. Пьезоэлектрические преобразователи и имитаторы Су-Нельсона помогают проверять стабильность передачи сигналов, их амплитуду, частоту выбросов, а также уровень шумов, искажений, чувствительность, скорость распространения звука, затухание и пр.
Специалистов АЭ по возможности размещают в отдельном помещении, с температурой от +15 до +30 ˚С, с надёжным источником переменного напряжения 220В и мощностью не менее 10 кВт.
Если акустико-эмиссионный контроль проводится не в обычном технологическом режиме, то далее объект нагружают в соответствии с утверждённым графиком. Чаще всего для этого проводятся гидравлические испытания. Непосредственно перед контролем в течение хотя бы 10–15 минут оценивают уровень акустического шума. В зависимости от этого, в соответствии с методикой АЭ-контроля, корректируются циклы и скорость нагружения. Нагружение должно нарастать плавно, с 10-минутной выдержкой на каждой промежуточной ступени.
В тех местах, где есть дефекты и напряжения, возникают упругие колебания – сигналы акустической эмиссии, которые и регистрируются датчиками АЭ. Частота этих сигналов может быть «разбросана» в широком диапазоне, от нескольких десятков до несколько сотен МГц. После преобразователя импульсы попадают на усилительный тракт, полоса пропускания которого ограничена. Это приводит к их некоторому искажению и приобретению двухполярного колебательного характера. Из-за этого длительность импульсов увеличивается – и они могут «сливаться» друг с другом. Если длительность двух следующих друга за другом импульсов меньше, чем интервал между ними, то акустическая эмиссия считается дискретной. В противном случае акустическую эмиссию называют непрерывной. Именно она чаще всего возникает в процессе пластической деформации и вязкого разрушения. Поскольку структура металла сама по себе состоит из случайно ориентированных зёрен, то разрушение каждого из них сопровождается излучением единичного импульса акустической эмиссии. Его параметры зависят от формы и размеров зерна. Возможности для разделения импульсов зависят от чувствительности и разрешающей способности аппаратуры.
Дополнительно к этому акустическую эмиссию оценивают по ряду первичных и вторичных параметров.
- Максимальная амплитуда (в дБ) и максимальное импульсное отклонение напряжения (тока) сигнала от первоначального уровня (в мкВ).
- Длительность фронта (нарастания) – это время с момента пересечения сигналом порогового значения (порога дискриминации) до времени достижения максимальной амплитуды сигнала. И, напротив, длительность спада – время с момента достижения максимальной амплитуды до момента уменьшения сигнала ниже порогового значения. Под порогом дискриминации понимается фиксированное либо регулируемое напряжение, приведённое ко входу аппаратуры. Если импульсы АЭ выше этого порога – то они регистрируются и обрабатываются. Если ниже – то пропускаются.
- Длительность импульса и число импульсов в единицу времени.
- Амплитудное распределение сигналов АЭ по времени.
- Количество зарегистрированных импульсов дискретной акустической эмиссии за период наблюдения.
- Количество зарегистрированных превышений сигналами АЭ заданного порога за период наблюдения.
- Отношение количества импульсов АЭ к периоду наблюдения.
- Энергия, которую выделяют импульсы АЭ и которую переносят упругие волны, распространяющиеся в металле. Один из ключевых энергетических параметров – MARSE (измеренная площадь по огибающей сигнала).
- Частотный, фазовый спектр импульсов и т.д.
При проведении акустико-эмиссионного контроля трубопроводов регистрируют выбросы – осцилляции сигналов выше порога дискриминации. Совокупность осцилляций выше порога за рассматриваемый промежуток времени объединяют в события. Чем больше импульсов за единицу времени – тем больше выбросов и событий, тем выше активность и тем выше скорость развития повреждений.
Обработка сигналов, как мы уже отмечали выше, осуществляется регистрирующим блоком многоканальной системы. Сигналы акустической эмиссии, источником которых служит локальная перестройка структуры металла, нужно отделить от помех, возникающих, например, при ударных воздействиях на трубопровод, работе электрооборудования и пр. Даже осадки в виде дождя или снега могут спровоцировать возникновение упругих колебаний, мешающих расшифровке сигналов АЭ.
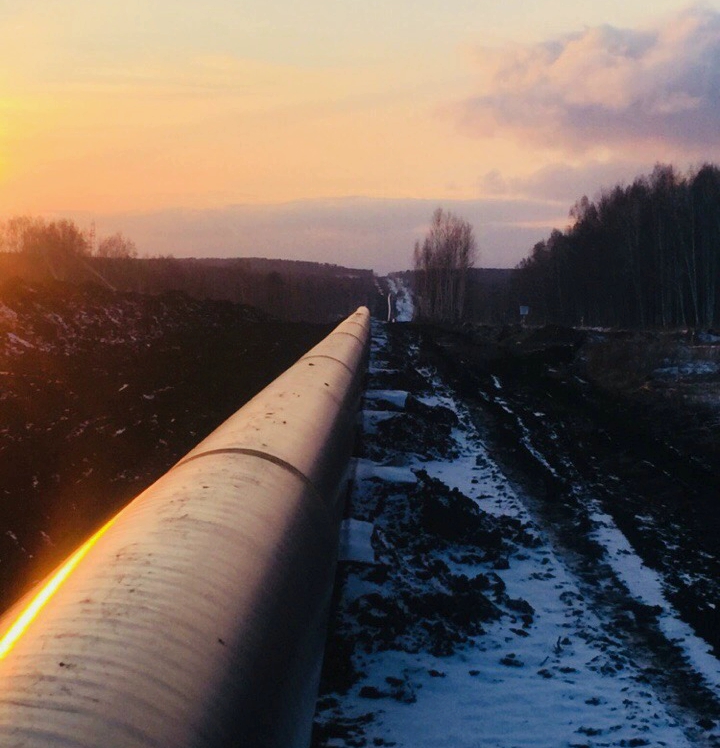
Интерпретация сигналов акустической эмиссии
В зависимости от свойств материала и протекающих в нём процессов импульсы акустической эмиссии подразделяются на несколько типов. Основной тип – релаксационный. В процессе разрушения снимаются локальные напряжения, вследствие чего возникает импульс с крутым фронтом. Это и есть релаксация – когда материал возвращается к первоначальном ненагруженному состоянию. В процессе ускоренного взаимного перемещения атомы отдаляются друг от друга с уменьшением силы взаимодействия. Образование трещин и состоит в разрыве межатомных связей и разрушением кристаллов. Энергия, накопленная для преодоления межатомного притяжения, высвобождается, что и приводит к импульсному возмущению – акустическому смещению среды в виде сферической продольной и поперечной волны, исходящей от места разрыва. Ввиду того, что с увеличением частоты возрастает и коэффициент затухания, высокочастотная составляющая сигнала быстро ослабевает. Когда волны падают на поверхность объекта, они отражаются и трансформируются, вследствие чего возникает поверхностная (рэлеевская) волна. Поскольку их амплитуда медленнее уменьшается с расстоянием, то именно поверхностные волны регистрируются преобразователями – приёмниками сигналов акустической эмиссии.Особенность трубопроводов заключается том, что многократные отражения разных типов волн от стенок накладываются друг на друга. «Волновая картина» при излучении сигналов акустической эмиссии подразделяется на ближнюю и дальнюю зону. Ввиду цилиндрической формы объекта уменьшение амплитуды сигналов в ближней зоне происходит не только из-за затухания, но и из-за геометрического расхождения импульса. Так, среднее значение коэффициента затухания в ближней зоне для стальных газопроводов оценивается в 2 дБ/м. Для заполненных нефтью магистральных трубопроводов – порядка 10 дБ/м. В дальней зоне геометрическое расхождение уже не играет такой роли – сигнал заполняет всё сечение трубы. В этом случае, в дальней зоне среднее значение коэффициента затухания для стальных газопроводов оценивается в 0,2 дБ/м. Для стальных нефтепроводов, заполненных нефтью или нефтепродуктом, он составляет порядка 1 дБ/м.
Что касается фильтрации полезных сигналов от механических шумов, то длительность последних существенно больше длительности импульсов, возникающих при образовании и росте дефектов. Механические шумы, как правило, низкочастотные. Частота не превышает 200 кГц. Адаптивная частотная фильтрация помогает идентифицировать на их фоне первичные полезные сигналы. Все они регистрируются центральным блоком, равно как и числом осцилляций – пересечений сигналами порогового уровня.
Обнаруженные источники АЭ классифицируются на 4 класса.
- I класс – пассивные источники. При обнаружении таких источников никаких срочных решений не принимают – но за динамикой их развития следят.
- II класс – активные источники. Их регистрируют, следят за их развитием и отображают в отчётах с рекомендациями по дополнительному дефектоскопическому контролю.
- III – критически активные источники. Помимо регистрации и дальнейшего анализа, такие источники АЭ, проводят подготовительные мероприятий на случай возможного сброса нагрузки.
- IV – катастрофически активные источники. При регистрации таких источников АЭ немедленно снижают нагрузку до нуля либо до уровня, при которой класс не опустится до II или хотя бы III класса. После этого трубопровод осматривают и проводят дополнительный дефектоскопический контроль другими видами (методами) НК.
Другая важная технологическая операция при обработке сигналов акустической эмиссии – определение координат источников АЭ. Этому может помешать, например, сильное затухание сигналов, на трубопроводах – наличие тройников, отводов, арматуры. Поскольку трубопровод – протяжённый объект, то для определения координат дефектов задействуются, как минимум, два преобразователя акустической эмиссии. Аппаратура фиксирует расстояние между двумя «соседними» ПАЭ и по разнице времени прихода сигнала на каждый из них определяет координаты дефекта. Помимо временного способа локализации, практикуется также амплитудный способ, когда координаты определяются не по разности времени прихода импульсов, а по отношению их амплитуд. В общем случае, чем ближе источник к датчику, тем выше амплитуда, и наоборот. Для определения местоположения источников непрерывных сигналов АЭ амплитудный способ предпочтительный. Для импульсов, напротив, он может оказаться неоптимальным ввиду переотражений, влияния пространственной ориентации дефекта и прочих посторонних факторов.
При этом встречаются задачи контроля, которые не предполагают точного определения координат дефектов. Достаточной может оказаться приблизительная оценка местоположения. В таких случаях можно обойтись одноканальной системой либо задействовать многоканальную систему, но в режиме зонной локации. Для трубопроводов, ввиду их протяжённости, такие решения зачастую эффективны.
Результаты акустико-эмиссионного контроля отражают в заключении с указанием наименования трубопровода, участка, его параметров, а также используемой аппаратуры. В заключении указывается модификация АЭ-системы, настройки её каналов и используемые преобразователи акустической эмиссии. Также при оформлении результатов контроля отражают параметры нагружения и приводят все зарегистрированные источники сигналов акустической эмиссии. Каждому источнику присваивается класс, плюс в заключении указывают его координаты и в подробностях приводят характеристики самих АЭ-сигналов, важных для интерпретации. Современное ПО позволяет дополнять протоколы акустико-эмиссионного контроля, куда, помимо текста и таблиц, встраивается инфографика, диаграммы, скриншоты с изображением эхограмм и пр.
На основании всех этих данных делаются выводы о техническом состоянии трубопровода. Дополнительно в заключении могут содержаться рекомендации по дальнейшему диагностическому обследованию. Правом оформлять и подписывать заключение по результатам АЭ-контроля обладают аттестованные специалисты II и III уровня.
Где купить аппаратуру для контроля трубопроводов методом акустической эмиссии
В числе партнёров "Дефектоскопист.ру" представлено одно из ведущих в РФ предприятий, которое специализируется на технологиях АЭ-контроля более 30 лет.НПО «Алькор». Научно-производственное объединение в городе Дзержинск Нижегородской области. Создано в 1991 году. Организация входит в Российское общество неразрушающего контроля и технической диагностики (РОНКТД) и Подкомитет №9 «Акустико-эмиссионные методы» Технического комитета №371 при Росстандарте. НПО «Алькор» занимается разработкой и серийным производством комплексов для акустико-эмиссионного контроля трубопроводов, конструкций зданий и сооружений, сосудов, ёмкостного оборудования и пр. Предприятие выпускает всю необходимую аппаратуру для АЭ-метода, от преобразователей акустической эмиссии и усилителей до блоков обработки информации и программного обеспечения. Система менеджмента качества сертифицирована по ISO 9001:2008. Оборудование НПО «Алькор» успешно применяется на объектах «Транснефти», «Роснефти», «Сургутнефтегаза», «ЛУКОЙЛ», «СИБУР» и др. Положительный опыт эксплуатации разработок подтверждается многочисленными отзывами. Также НПО «Алькор» располагает собственной аттестованной лабораторией, которая выполняет акустико-эмиссионный контроль трубопроводов и сосудов по всей стране. Коммерческий отдел: +7 (8313) 25-26-10, +7 (920) 074-13-23, alcor@alcor.pro.
Многие из партнёров «Дефектоскопист.ру» предоставляют форумчанам хорошие скидки. Берегите бюджет своей лаборатории – и покупайте оборудование неразрушающего контроля только у надёжных поставщиков!