Акустико-эмиссионный контроль резервуаров вертикальных стальных (РВС)
Акустико-эмиссионный контроль резервуаров вертикальных стальных (РВС) проводится в рамках частичного либо полного обследования их технического состояния. Метод акустической эмиссии применяется параллельно с нагружением резервуара продуктом (без вывода из эксплуатации) либо с гидравлическими испытаниями. Неразрушающему контролю (НК) при этом подвергается стенки (пояса) и днища, включая сварные соединения и основной металл. Резервуары вертикальные стальные считаются наиболее опасными из всех опасных производственных объектов (ОПО), которые задействуются в технологической схеме нефтедобычи. В резервуарных парках сосредоточено большое количество нефти и нефтепродуктов, а потому к их соответствию нормам промышленной безопасности предъявляются повышенные требования. Акустико-эмиссионный контроль позволяет выявлять свищи, трещины, протечки, образование коррозии в области трещины, отслоение шлаковых включений и прочие развивающиеся дефекты и разрушения. Одно из ключевых преимуществ метода акустической эмиссии – высокая чувствительность, возможность регистрации приращения трещины всего на десятые доли миллиметра. Предельная чувствительность может достигать порядка 1*10^(-6) кв. мм (1 кв. мкм), что соответствует приращению трещины протяжённостью 1 мкм на 1 мкм.Содержание:
Преимущества и ограничения метода акустической эмиссииДля чего проводится акустико-эмиссионный контроль РВС
Оборудование для акустико-эмиссионного контроля
- Преобразователи акустической эмиссии
- Усилители
- АЭ-комплексы
Порядок проведения АЭ-контроля резервуаров
- Установка преобразователей акустической эмиссии на РВС
- Нагружение резервуара
- Анализ сигналов акустической эмиссии
- Оформление результатов АЭ-контроля
Где купить аппаратуру для АЭ-контроля и пройти обучение
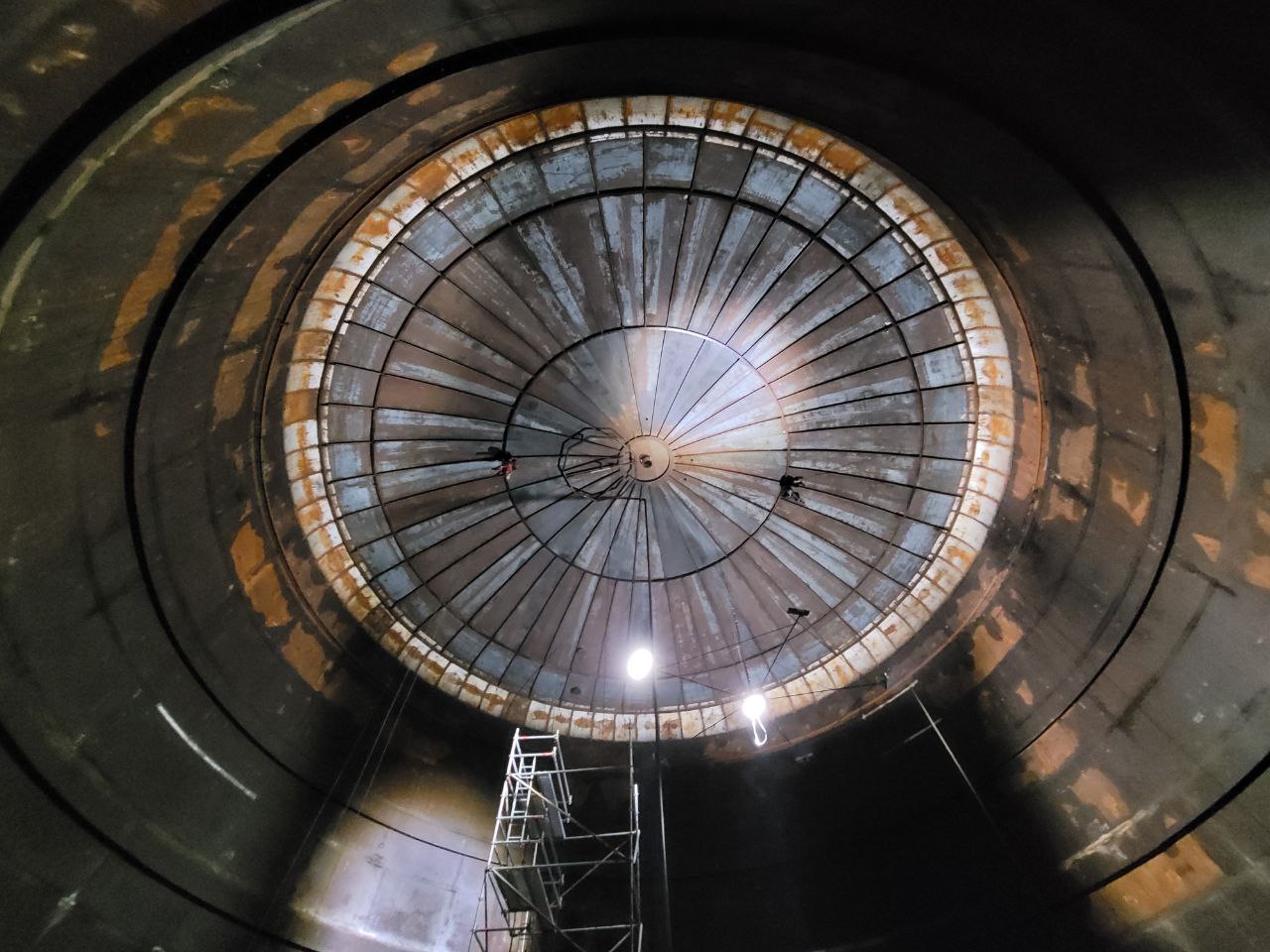
Метод акустической эмиссии предполагает анализ амплитудных и временных параметров каждого зарегистрированного сигнала, включая:
- амплитуду сигнала – максимальное значение электрического импульса акустической эмиссии (измеряется как максимальное, так и минимальное значение электрического напряжения);
- уровень АЭ – среднее квадратическое значение сигналов за определённый период времени;
- длительность сигнала – время между его началом и концом, например, на определённом значении амплитуды либо по превышению заданного порога;
- время нарастания импульса акустической эмиссии – время между началом сигнала и его максимальным значением;
- время спада импульса акустической эмиссии – время между его максимальным значением и концом сигнала;
- конец импульса акустической эмиссии – его окончание, определённое по последнему пересечению порога;
- общее число импульсов дискретной АЭ за определённый интервал времени;
- суммарную АЭ – количество превышений сигналом акустической эмиссии заданного порога, зарегистрированных за определённый интервал времени;
- активность АЭ – отношение числа импульсов к единице времени;
- энергию АЭ в заданной полосе частот в течение определённого интервала времени;
- MARSE – измеренную площадь под огибающей сигнала (аббревиатура расшифровывается как Measured Area of the Rectified Signal Envelope);
- интервал контроля пика – для разделения «соседних» амплитудных пиков, корректной идентификации пика сигнала и правильного определения максимальной амплитуды сигнала;
- интервал контроля длительности сигнала – для разделения одного сигнала от другого и определения момента, когда амплитуда сигнала опускается ниже заданного порога;
- интервал контроля конца сигнала – для остановки сбора данных после конца сигнала АЭ, что помогает, например, исключить отражение волн напряжения от границы раздела сред;
- амплитудное распределение сигналов акустической эмиссии по времени, количество зарегистрированных сигналов АЭ, отношение этого количества к периоду наблюдения, суммарный счёт, разность времён прихода (РВП) и т.д.
Источниками сигналов акустической эмиссии могут быть локальные разрушения, пластическая деформация металла, изменение его кристаллической решётки (фазовые превращения), утечки (по мере пульсации и схлопывания пузырьков в жидкости или газе), пристеночные пульсации давления и акустические колебания стенки РВС (из-за нестабильного давления в жидкости или газе), трение берегов трещины, механические контакты плохо закреплённых элементов конструкции резервуара и пр. Два основных условия для появления сигналов акустической эмиссии – локальность (изменения структуры должны быть ограничены в пространстве) и динамичность (переход из одного структурного состояния в другое должен осуществляться достаточно быстро). Образование и рост трещины – типичный пример такого процесса, протекающего с высокой скоростью в ограниченном объёме материала.
Преимущества и ограничения применения АЭ-метода на РВС
Акустико-эмиссионный контроль повсеместно применяется для очередного и внепланового технического диагностирования резервуаров вертикальных стальных, в том числе – в рамках экспертизы промышленной безопасности (ЭПБ) и непрерывного интегрального мониторинга. АЭ-метод предусмотрен во многих нормативных технических документах (НТД), конструктивно-проектной документации на РВС и т.д. Широкому распространению данному пассивному методу акустического контроля способствовали следующие его достоинства.- Высокая чувствительность к небольшим дефектам и активным коррозионным процессам типа прогрессирующего утонения стенки или охрупчивания. Высокая выявляемость трещин как наиболее опасных нарушений сплошности основного металла и сварных швов. Метод акустической эмиссии эффективен и для выявления свищей, истечения рабочей среды (к примеру, утечки нефти или нефтепродуктов) через сквозные отверстия в резервуаре, для обнаружения протечек в уплотнениях, арматуре, фланцевых соединениях, заглушках и т.д. Современные технологии акустико-эмиссионного контроля позволяют не только выявлять, но и классифицировать дефекты не по размерам (как в большинстве других методов НК), а по степени их опасности. Всё это даёт возможность оценивать их реальное влияние на техническое состояние резервуара. И что тоже важно – выявляемость дефектов не зависит от их пространственной ориентации и местоположения. В том же ультразвуковом контроле эхо-импульсным методом, для сравнения, большую роль играет ориентация дефекта относительно луча, шероховатость его поверхности, коэффициент формы, положение в сечении сварного шва, угол скоса кромок соединяемых элементов и т.д. Все эти и многие другие параметры могут серьёзно повлиять на выявляемость.
- Применение преобразователей, которые неподвижно закрепляются на объекте (к примеру, на стенках резервуара). Не нужно сложной и дорогостоящей подготовки всей поверхности объекта – для контроля РВС нужно зачистить лишь отдельные «пятаки» для установки ПАЭ. Акустико-эмиссионный контроль не предполагает использования сканирующих устройств. Стабильный акустический контакт, равномерное усилие прижима преобразователя к поверхности РВС, влияние её шероховатости и волнистости – всё это в методе акустической эмиссии решается намного проще, чем в том же контактном способе эхо-импульсного метода УЗК. При этом обеспечивается выявляемость дефектов даже на тех участках (элементах конструкции), которые остались под теплоизоляционной оболочкой, лакокрасочным или иным покрытием и находятся на большом расстоянии от ближайшего преобразователя акустической эмиссии. Допустимое расстояние между датчиками, к слову, зависит от массы параметров, начиная акустическими свойствами металла и заканчивая конструктивными особенностями РВС, и может достигать 15 м и больше.
- Сокращение расходов на дефектоскопический контроль другими физическими методами – ультразвуковым, радиографическим, тепловым и т.д. На самом деле, сравнение акустико-эмиссионного контроля с УЗК, РК или иным видом (методом) неразрушающего контроля – не совсем корректно. Каждый из них имеет свои преимущества и ограничения, каждый решает свои задачи. Акустико-эмиссионный контроль отлично дополняется ультразвуковым, радиографическим, магнитопорошковым, капиллярным и другими. Причём зачастую метод АЭ позволяет сократить затраты на проведение дополнительного дефектоскопического контроля: УЗК, РК, ПВК и МПК проводят на тех участках, где зафиксированы источники сигналов акустической эмиссии (если такая возможность предусмотрена в руководящих нормативных документах, технической документации на ОПО и в программе испытаний). Сочетание акустико-эмиссионного контроля с другими методами НК существенно повышает достоверность обнаружения дефектов. При этом оценивают остаточный ресурс (суммарную прогнозируемую наработку резервуара от момента контроля его технического состояния до перехода в предельное состояние) и принимают решение о дальнейшей эксплуатации вертикальных стальных резервуаров.
- Возможность проведения контроля без вывода РВС из эксплуатации и мониторинга развития дефектов в режиме реального времени. Акустико-эмиссионный контроль резервуаров вертикальных стальных может проводиться как периодически (например, в рамках планового выполнения работ по техническому диагностированию), так и в непрерывном режиме «интегрального мониторинга». В последнем случае для АЭ-контроля применяются стационарные многоканальные комплексы типа «Ресурс-2000» (разработчик – НПО «Алькор», Дзержинск), которые могут интегрироваться в центральные системы мониторинга и диагностики технического состояния опасных производственных объектов, не только одного конкретного РВС.
- Высокие затраты на проведение гидравлических или пневматических испытаний, необходимых для нагружения РВС. В целях сокращения расходов была разработана технология, по которой напряжённо-деформированное состояние контролируемой поверхности создаётся только на отдельных участках с наиболее высокой вероятностью возникновения дефектов. Для этого на интересующий участок воздействуют охладителем, в качестве которого используется сухой лёд. Сублимация сухого льда происходит при температуре -70 градусов Цельсия. Такой способ упругой деформации охлаждением поверхности помогает добиваться высокой выявляемости дефектов и уменьшить влияние ложных акустических шумов. Низкотемпературный способ локального нагружения, к примеру, стенок или днища РВС, избавляет от необходимости нагружать весь резервуар, повышает безопасность и производительность работ по акустико-эмиссионному контролю. Для регистрации сигналов АЭ используются преобразователи в специальном исполнении, устойчивые к отрицательным температурам. Подробнее о низкотемпературном нагружении для АЭ-контроля можно почитать в публикациях сотрудников Уфимского государственного нефтяного технического университета.
- Необходимость согласованного проведения всех этапов контроля с заказчиком, а также с организацией, отвечающей за проведение гидравлических (или пневматических) испытаний, а возможно, и с организацией, выполняющей ЭПБ, и т.д.
- Сложность расшифровки сигналов, наличие мешающих помех и шумов. С одной стороны, метод акустической эмиссии связан с меньшим количеством ограничений, обусловленных свойствами и кристаллической структурой контролируемого материала. В этом плане с тем же ультразвуковым контролем эхо-методом всё немного сложнее, потому что прозвучивание, скажем, аустенитных сталей часто сопровождается высоким уровнем шумов. С другой стороны, сами по себе сигналы акустической эмиссии – шумоподобные, ввиду того что импульсы АЭ являются случайными импульсными событиями, которые, в свою очередь, сами приводят к возникновению затухающей последовательности импульсов. Выделение полезных сигналов, особенной малой амплитуды, может оказаться трудной задачей. Правда, по мере развития дефекта и достижения критических размеров, амплитуда сигналов увеличивается, а сами они регистрируются чаще. И всё это повышает вероятность выявления таких источников сигналов АЭ – потенциально опасных дефектов. Акустико-эмиссионный контроль резервуаров вертикальных стальных (РВС) обычно проводится в рабочем диапазоне частот от 100 до 500 кГц (в зависимости от конкретных условий и возможностей аппаратуры полоса частот может составлять от 10 кГц до 1 МГц). Распространение упругих колебаний (продольных, поперечных, поверхностных, нормальных волн) в металле – сложный процесс, который определяется особенностями отражения, трансформации, преломления волн, интерференции и зависит от резонансных свойств приёмно-усилительного тракта, механических шумов, помех и пр. Импульсы АЭ представляют собой суперпозиции разных волновых компонентов. Так, при «скачке» трещины поперечные (сдвиговые) волны распространяются под углами 45 и 135 градусов к направлению её роста. Продольные волны – излучаются в направлении, перпендикулярном к плоскости этой самой трещины. В современных комплексах АЭ-контроля реализуется большое количество решений – и в аппаратной части, и по части ПО – для шумоподавления, отсечки помех, фильтрации ложных сигналов и достижения по возможности наиболее высокого отношения сигнал-шум. Кроме того, добиться уменьшения уровня шумов и помех можно при должной дисциплине непосредственно при проведении испытаний и акустико-эмиссионного контроля. Важно, чтобы параллельно с этим на объекте не велось никаких строительно-монтажных работ и чтобы было исключено влияние постороннего работающего оборудования, вибрационных, термодинамических нагрузок и т.д. Никто не должен ходить по площадкам обслуживания на РВС, сварочные и монтажные работы должны быть приостановлены. Даже передвижение автотранспорта вблизи резервуара желательно ограничить. В отстройке от фоновых помех может помочь задание некоего ненулевого порога амплитуды сигналов, ниже которого последние могут считаться шумами и не подлежать рассмотрению. Причём современное ПО для акустико-эмиссионного контроля позволяет настраивать не только фиксированный, но и плавающий порог аппаратуры (выраженный в вольтах порог, при достижении которого сигналы подлежат регистрации и обработке). Последний вариант лучше подходит при наличии меняющихся помех большой амплитуды. Плавающий порог зависит от среднего уровня сигнала и может автоматически корректироваться индивидуально по каждому акустическому каналу.
- Высокие требования к квалификации персонала. Каждый вид (метод) неразрушающего контроля по-своему сложен (даже визуальный и измерительный контроль), но метод акустической эмиссии объективно считается одним из самых трудных для освоения.
- Некоторые ограничения информативности результатов контроля. Сложность или невозможность определения типа дефекта, его размеров, глубины залегания и пр. При использовании зонной локации – сравнительно низкая точность определения местоположения дефектов. Как было отмечено выше, всё это компенсируется тем, что акустико-эмиссионный контроль отлично дополняется иными физическими методами дефектоскопии для более детального изучения обнаруженных дефектов. Тем более что АЭ-контроль позволяет оценить главное – степень их опасности и влияние на техническое состояние РВС.

Когда и для каких задач проводится акустико-эмиссионный контроль РВС
АЭ-контроль проводится при частичном либо полном обследовании резервуаров вертикальных стальных в рамках экспертизы промышленной безопасности, а также перед вводом РВС в эксплуатацию после строительства или капитального ремонта. В соответствии со стандартом СА-03-008-08 «Резервуары вертикальные стальные сварные для нефти и нефтепродуктов. Техническое диагностирование и анализ безопасности», при отсутствии возможности освободить резервуар от продукта для его полного обследования, последнее разрешается заменять обследованием частичным, но с обязательным проведением акустико-эмиссионного контроля стенок и днища. АЭ-контроль проводится параллельно с испытанием РВС на прочность наливом хранимого продукта. Это позволяет проводить техническое диагностирование резервуара без вывода из эксплуатации, а порой и без существенного изменения режима его работы.Для этого эксплуатируемый РВС должен быть наполнен продуктом. Начальный уровень налива должен быть не более 60% от максимального рабочего уровня. В процессе проведения акустико-эмиссионного контроля резервуар наполняют продуктом до высоты, соответствующей 105% максимального уровня наполнения за предшествующие испытаниям 12 месяцев эксплуатации. Если по техническим причинам это невозможно, то нагружение осуществляют на максимальном доступном уровне с его циклическим изменением.
Аппаратура для неразрушающего контроля РВС методом акустической эмиссии
Для акустико-эмиссионного контроля резервуаров вертикальных стальных используются комплексы акустико-электронных устройств, которые принимают, усиливают, идентифицируют и обрабатывают сигналы акустической эмиссии, определяют, регистрируют их параметры и пр. Для АЭ-метода применяется большое количество технических средств.
Преобразователи акустической эмиссии (ПАЭ)
Акустико-эмиссионный преобразователь представляет собой пьезоэлектрическое устройство обнаружения, которое преобразует движение частиц, произведённое упругой волной, в электрический сигнал. Конструктивно ПАЭ имеет сходство с совмещёнными прямыми пьезоэлектрическими преобразователями для ультразвуковой дефектоскопии (УЗД) и толщинометрии (УЗТ). В конструкции преобразователя акустической эмиссии есть те же ключевые элементы:
- пьезопластина, которая трансформирует акустические колебания в электрические сигналы;
- электрические выводы (электроды, по которым поступают электрические сигналы);
- протектор, защищающий пьезопластины от изнашивания и блуждающих электрических токов при установке ПАЭ на массивных металлоконструкциях, к коим относятся и сварные вертикальные цилиндрические резервуары;
- демпфер, уменьшающий длительность свободных колебаний пьезопластины и обеспечения равномерной чувствительности в широком диапазоне частот. Резонансные преобразователи без демпфирования отличаются большей чувствительностью, но позволяют регистрировать сигналы только в узком частотном диапазоне вблизи резонансной частоты, поскольку передний и задний фронты импульсов получаются сильно затянутыми;
- корпус, обеспечивающий прочность всей конструкции ПАЭ и защищающий его от агрессивных внешних воздействий;
- разъём для подключения коаксиального кабеля.
Важная характеристика преобразователя акустической эмиссии – коэффициент преобразования в режиме приёма как отношение амплитуды электрического напряжения к амплитуде поступающей на ПАЭ акустической волны. Чем выше этот коэффициент, тем выше чувствительность – и тем сильнее возникающие электрические сигналы. Чувствительность ПАЭ оценивается также по коэффициенту двойного преобразования – то есть по отношению амплитуды электрического сигнала, поступающего с преобразователя, к амплитуде электрического сигнала, который на него подаётся.
Другой важный параметр преобразователей для акустико-эмиссионного контроля – амплитудно-частотная характеристика (АЧХ), которая указывает на зависимость коэффициента двойного преобразования от частоты и на чувствительность к сигналам разной частоты. У каждого преобразователя есть свой диапазон частот (полоса пропускания), в пределах которого он эффективен и допускается к использованию. Полоса пропускания включает в себя частоты, на которых коэффициент двойного преобразования уменьшается от максимального значения не более, чем в 2 раза (амплитуда сигналов отличается от максимума не более чем на 6 дБ). Наиболее широкой полосой пропускания обладают широкополосные ПАЭ, у которых её верхний порог частоты может превышать нижний более чем в 5 раз. Поскольку сигналы акустической эмиссии имеют заведомо неизвестные, существенно отличающиеся между собой частоты – то широкополосные преобразователи акустической эмиссии зачастую наиболее эффективны для акустико-эмиссионного контроля резервуаров и иных опасных производственных объектов. Такие ПАЭ в наименьшей степени влияют на искажение импульсов.
Усилители
Подразделяются на основные и предварительные. Предусилитель может подключаться как отдельное устройство (по кабелю длиной не более 0,5 м) или быть интегрированным в корпус ПАЭ. Предусилитель может быть дополнен полосовым фильтром для отсеивания низко- и высокочастотных составляющих электрических колебаний. К примеру, такой фильтр может пропускать колебания только в диапазоне частот 10–700 кГц, тем самым отсекая низкочастотные механические колебания, обусловленные не развитием дефектов, а различными вибрациями вследствие работы механического оборудования, радиопомех и т.д. Основной усилитель настраивается отдельно и предназначен для дополнительного усиления сигналов, которые преодолели порог дискриминации.
АЭ-системы
Для акустико-эмиссионного контроля сварных вертикальных цилиндрических резервуаров применяются многоканальные комплексы, в составе которых предусмотрены средства регистрации, идентификации и обработки сигналов АЭ – плата регистрации, детектор, автоматический таймер, компаратор (определяет порог селекции), коммутатор, аналого-цифровой преобразователь (АЦП, записывает изменяющиеся значения амплитуды напряжения сигналов в виде закодированных цифр и передаёт их на ПК), персональный компьютер со специализированным ПО и т.д. Аппаратура для акустико-эмиссионного контроля резервуаров вертикальных стальных должна работать в широком динамическом диапазоне (100 дБ и более), обеспечивать возможность выделения единичных сигналов акустической эмиссии малой амплитуды, регистрировать их даже при ускоренном росте трещины, что сопровождается интенсивным потоком импульсов относительно больших амплитуд.
Для подключения сразу нескольких преобразователей акустической эмиссии к блоку сбора и обработки данных используются специальные разветвительные кабели. Для организации непрерывного интегрального мониторинга стационарные АЭ-системы дополняют модулями сбора данных и GSM-модемами для передачи информации на сервер. В современных комплексах также предусматривается набор встроенных сервисных устройств типа контроллеров, параметрических каналов, встроенных электронных имитаторов для поддержания работоспособности всей системы. Параметрические каналы могут параллельно с регистрацией сигналов акустической эмиссии фиксировать для каждого из них какой-либо дополнительный параметр. Например, величину давления в резервуаре в процессе испытаний.
Примеры комплексов для акустико-эмиссионного контроля - «Ресурс-2000», «Эксперт-2020», «Эксперт-2014», «ЮНИСКОП», A-Line-32D, A-Line DDM-1, A-Line DDM-2, AEC-USB, серия «Малахит» (АС-12А, АС-15А, АС-15/2) и др. Наиболее известные разработчики – НПО «Алькор», «Интерюнис-ИТ», НПФ «Диатон» и др.
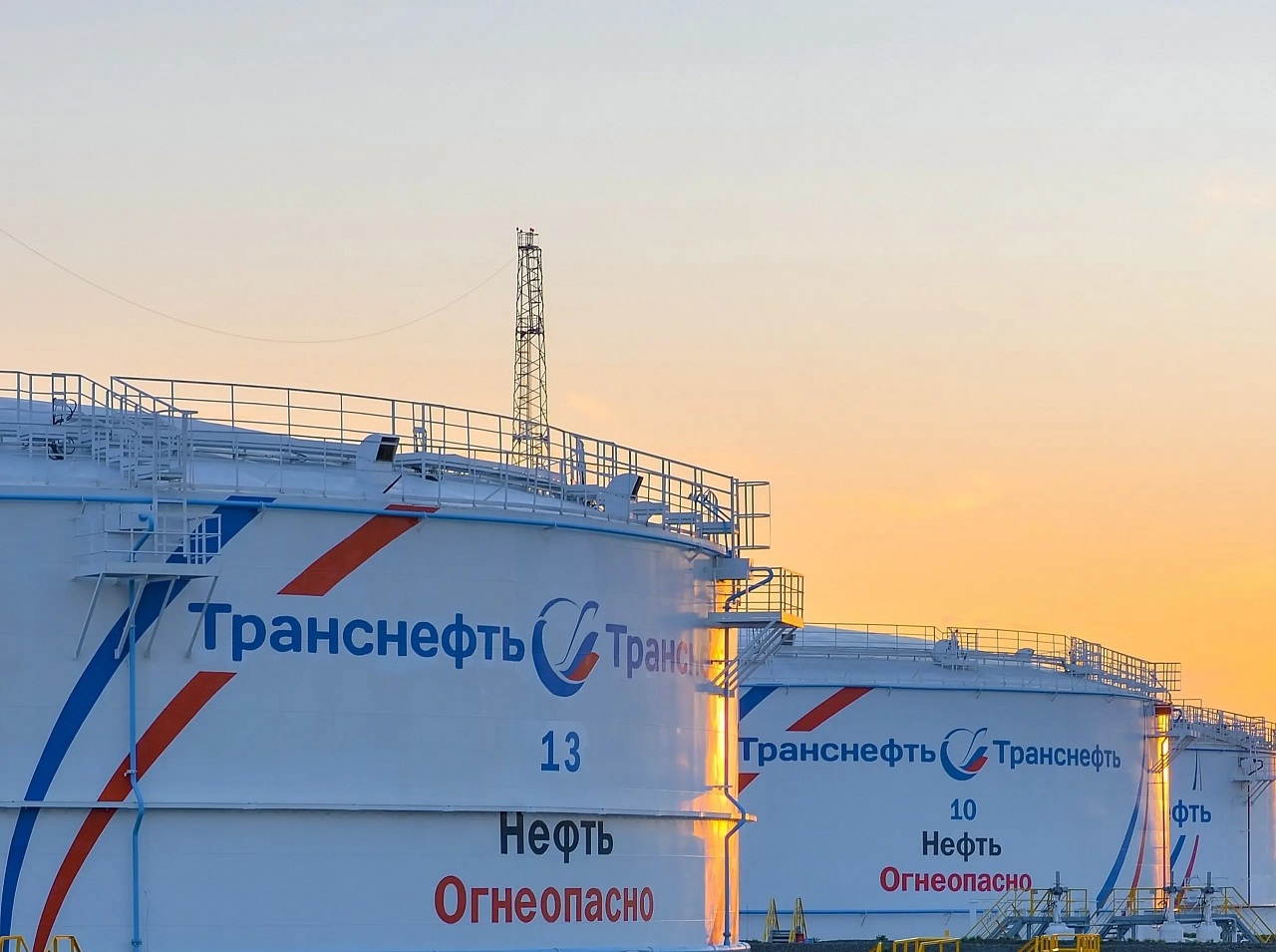
Порядок проведения акустико-эмиссионного контроля РВС
Работы должны выполняться в соответствии с руководящими нормативными техническими документами и, в частности, с программой работ по АЭ-контролю. Её разработкой и утверждением занимаются аттестованные специалисты акустико-эмиссионного контроля II и III уровня, начальник лаборатории неразрушающего контроля (ЛНК), заказчик работ и пр. Перед составлением программы работ по АЭ-контролю собирают и обрабатывают информацию о вертикальном стальном резервуаре, включая:
- проектно-конструкторскую и техническую документацию;
- фактические условия и режим эксплуатации (если таковая имела место быть);
- конструктивные особенности, особенности изготовления, монтажа, строительства;
- сведения о ранее выполненных испытаниях;
- местоположение сварных соединений;
- сведения о конкретной марке металла, из которого изготовлен резервуар вертикальный стальной. Для корректного проведения акустико-эмиссионного контроля анализируется информация об акустических свойствах сплава, включая его скорость распространения ультразвуковых колебаний, коэффициент затухания, плотность и пр. Часть данных могут заимствоваться из научно-справочной литературы.
- параметры шумов. Марки стали для разных элементов конструкции РВС подбираются в соответствии с ГОСТ 31385-2023 «Резервуары вертикальные цилиндрические стальные для нефти и нефтепродуктов. Общие технические условия». На практике для строительства РВС часто используется сталь марок 09Г2С, Ст3сп, 08Х13, 08Х18Н10, 12Х18Н9 и др. Методические приёмы акустико-эмиссионного контроля наиболее распространённых сталей хорошо известны, в том числе – предполагаемый уровень шумов и способы борьбы с ними. Все эти наработки используются для составления технологии АЭ-контроля при строительстве, монтаже, капитальном ремонте, реконструкции, плановом техническом диагностировании РВС;
- тип и параметры преобразователей акустической эмиссии. Требования к ПАЭ, которые применяются на опасных производственных объектах, отражены, например, в РД 03-300-99. К параметрам преобразователей акустической эмиссии относится их амплитудно-частотная характеристика, коэффициент электроакустического преобразования, рабочий диапазон температур, доступная длина подключаемого кабеля и так далее;
- количество ПАЭ, схема их установки на РВС и тип используемой для этого контактной жидкости. Закреплённые на поверхности объекта преобразователи акустической эмиссии образуют так называемую антенну, которая рассчитывается таким образом, чтобы обеспечить уверенный приём сигналов на всей зоне контроля. В качестве контактной среды для создания акустического контакта с поверхностью РВС применяется моторное масло, глицерин, эпоксидная смола (без отвердителя), специальные гели и другие жидкости. Обеспечение безопасного доступа к поверхности на РВС для установки ПАЭ – задача заказчика. Для этого могут использоваться автовышки или иные подъёмные механизмы, возводиться строительные леса и пр. При необходимости заказчиком предоставляется дополнительный персонал, который вырезает «окна» в теплоизоляции и зачищает поверхность для закрепления ПАЭ от краски и иных покрытий. Шероховатость не должна превышать Rz 40 мкм;
- требования к центральному блоку (прибора, комплекса) для акустико-эмиссионного контроля. Для акустико-эмиссионного контроля резервуаров вертикальных стальных применяются как переносные, так и стационарные приборы. В блоке должно быть предусмотрено достаточное количество акустических каналов, сам он должен поддерживать требуемый диапазон частот, обладать высоким быстродействием, широким динамическим диапазоном, соответствовать температуре окружающей среды, при которой проводятся работы по АЭ-контролю. Уровень собственных шумов приёмно-усилительного тракта должен быть как можно ниже (напряжение до 5 мкВ). Максимальная скорость регистрации в каждом отдельном акустическом канале у наиболее продвинутых систем может достигать 20 000, 40 000 или даже 150 000 событий в секунду (точное значение зависит от количества задействованных одновременно каналов). Эффективность акустико-эмиссионного контроля во многом зависит от того, какое программное обеспечение (ПО) реализовано в многоканальном комплексе, насколько оно удобное, гибкое в настройках, каким функционалом обладает, в каком виде генерирует отчёты (протоколы) по результатам испытаний – и так далее. К важным параметрам многоканальных комплексов для акустико-эмиссионного контроля относится количество акустических каналов, диапазон рабочих частот, доступные цифровые полосовые фильтры, типы доступных ПАЭ, регистрируемые параметры импульсов АЭ, программируемые параметры, возможность отображения источников АЭ на чертеже (модели) РВС, форма журнала для регистрации событий, настройки для защиты от несанкционированного доступа и т.д. Для акустико-эмиссионного контроля резервуаров вертикальных стальных и иных опасных производственных объектов применяются многоканальные комплексы, утверждённые в качестве типа средств измерений и внесённые в Государственный реестр СИ РФ. Соответственно, комплексы подлежат поверке, как минимум, раз в год;
- порядок и результат калибровки системы. После установки преобразователей акустической эмиссии на резервуаре вертикальном стальном проверяют их работоспособность при помощи имитатора Су-Нильсена с ломающимся графитовым стержнем диаметром 0,3–0,5 мм либо при помощи пьезоэлектрических преобразователей с генератором импульсов возбуждения частотой 1–100 Гц. Калибровка и проверка работоспособности аппаратуры для акустико-эмиссионного контроля выполняются для того, чтобы определить затухание и скорость распространения ультразвука в контролируемом материале, подтвердить чувствительность, стабильность передачи сигналов, оценить уровень шумов, искажений и прочие важные параметры. Кроме того, имитатор Су-Нильсена (излом карандаша) и ПЭП с генератором импульсов возбуждения помогают определять затухание, скорость распространения звука в материале и оценивать, правильно ли подобрано расстояние между преобразователями, то есть таким образом, чтобы сигнал акустической эмиссии в любом месте контролируемой зоны фиксировался минимальным количеством ПАЭ, достаточным для определения его координат. Амплитуда сигнала от излома карандаша при этом должна в 1,5 раза превышать порогового напряжения, которое устанавливается в ходе настройки аппаратуры с разрешением 1 дБ;
- описание процедуры испытаний, с указанием испытательного давления, графика изменения нагрузки, времени выдержки, температуру и прочие параметры нагружения. Непосредственно на время проведения акустико-эмиссионного контроля работы на близкорасположенных объектах рекомендуется приостановить – чтобы избежать возникновения шумов и помех, которые могут помешать анализу сигналов АЭ;
- система классификации источников сигналов акустической эмиссии и критерии оценки технического состояния контролируемого РВС. С учётом этого подбирается форма протокола, который заполняется по результатам акустико-эмиссионного контроля;
- требования к квалификации персонала, который будет проводить АЭ-контроль.
Установка преобразователей акустической эмиссии на РВС
Разнесение ПАЭ по поверхности сварного вертикального цилиндрического резервуара зависит от затухания ультразвука в металле (коэффициент затухания выше в сварных швах и на участках с изменением толщины) и требуемой точности локализации источников АЭ (чем она выше, тем больше датчиков потребуется). Контролируемую поверхность разделяют на отдельные участки и устанавливают ПАЭ группами. При использовании вспомогательных групп ПАЭ это помогает делать пространственную селекцию выявленных источников шума ещё точнее. Перед установкой преобразователя наносят контактную среду, например, эпоксидную смолу. Для закрепления ПАЭ на стенках и днище РВС удобно использовать магнитные держатели. При необходимости обеспечить акустический контакт между ПАЭ и отдалённой поверхностью объекта применяются акустико-эмиссионные волноводы.
После установки каждый преобразователь акустической эмиссии проверяют при помощи пьезоэлектрического преобразователя, возбуждаемого генератором, либо имитатора Су-Нильсена. Имитационный импульс АЭ должен соответствовать частотному диапазону используемой для контроля аппаратуры. Амплитуда сигналов по каждому акустическому каналу не должна отличаться от средней амплитуды для всех каналов более чем на ±3 дБ. Коэффициент усиления и порог амплитудной дискриминации подбираются для акустических каналов таким образом, чтобы сигналы АЭ соответствовали ожидаемому диапазону амплитуд. Главное – обеспечить неискажённую передачу сигналов акустической эмиссии и добиться того, чтобы за 100 секунд в каждом канале было не больше одного выброса помех.
При этом чувствительность разных групп преобразователей акустической эмиссии может отличаться, если это предусмотрено технологией контроля. При наличии такого разброса – сведения о нём отображаются в протоколе и отчёте по результатам акустико-эмиссионного контроля.
Непосредственно перед началом испытаний проверяют корректность всех настроек, фильтров и измерение параметров сигналов АЭ, перечисленных выше (амплитуда, MARSE, порог и пр.). Дополнительно проверяют корректность определения координат источников АЭ. При недостаточно высокой точности определения координат изменяют расположение ПАЭ, расстояние между ними и пр. Если акустико-эмиссионный контроль резервуара выполняется параллельно с гидравлическими испытаниями, то настройка аппаратуры производится после его заполнения водой. По завершении настройки, до перехода непосредственно к рабочему испытанию, в течение 15 минут проверяют шумовой фон – для того, чтобы убедиться, что шумы не превышают заданный порог.
Нагружение РВС
Схема и режим нагружения подбираются таким образом, чтобы создать в резервуаре напряжённое состояние, аналогичное тому, которое возникает в процессе эксплуатации. Испытания при акустико-эмиссионном контроле сварных вертикальных цилиндрических резервуаров проводятся в два этапа – предварительные испытания и рабочие испытания. Первые проводятся для того, чтобы:
- проверить работоспособность всей аппаратуры для АЭ-контроля,
- уточнить уровни шумов,
- скорректировать порог амплитудной дискриминации и настройки фильтров,
- выявить «ложные сигналы», например, в тех местах, где имеются точки крепления различных элементов (опоры, элементы жёсткости, вспомогательные сооружения и пр.).
Нагружение выполняется ступенями, по заранее утверждённому графику, с выдержкой на каждой из них (в среднем в течение 10 минут). Нагружение должно быть плавным, чтобы избежать возникновения интенсивных помех.
Время выдержки максимального давления для РВС в эксплуатации не превышает 5 минут, для строящихся РВС – зависит от толщины стенки и может достигать 10 минут и более. При акустико-эмиссионном контроле вертикальных стальных резервуаров, которые проходят испытания под налив, максимально допустимый уровень заполнения должен составлять не менее двух часов.
При самом первом нагружении вновь изготовленных резервуаров, которые ещё не проходили термообработку сварных соединений после сварки, могут быть зафиксированы сигналы, связанные не с развитием дефектов, а с выравниванием напряжений в металле. В таких случаях регистрируют только те сигналы акустической эмиссии, которые существенно превышают порог амплитудной дискриминации (не менее чем на 20 дБ), и проводят повторный контроль.
В течение всего цикла нагружения РВС ведётся мониторинг давления и температуры.

Анализ данных
Специалисты АЭ в непрерывном режиме наблюдают обзорную картину поступающих сигналов акустической эмиссии на экране монитора. Зафиксированные источники сигналов акустической эмиссии классифицируют на 4 класса (см. ПБ 03-593-03, ГОСТ Р 52727-2007) в соответствии с выбранной системой классификации.
- I класс – пассивные источники. К этой категории относятся неопасные дефекты, которые регистрируют для анализа динамики последующего развития.
- II класс – активные источники. Эта категория соответствует развивающимся, умеренно опасным дефектам. В процессе контроля следят за их развитием, а сведения о них в отчёте дополняют рекомендациями по контролю иными физическими методами дефектоскопии.
- III класс – критически активные источники. Само собой, их тоже регистрируют и отслеживают в процессе дальнейшего АЭ-контроля, плюс предпринимают подготовительные меры для возможного сброса нагрузки.
- IV – катастрофически активные источники. При регистрации такого источника АЭ нагрузку немедленно сбрасывают до нуля либо до величины, при которой он будет соответствовать II или III классу. После этого переходят к осмотру участка, на котором обнаружен этот источник. При необходимости – проводят дополнительный дефектоскопический контроль.
Критерии, по которым оцениваются параметры сигналов акустической эмиссии и на основании которых оценивается техническое состояние резервуара, зависят от выбранной системы классификации. Система классификации источников АЭ прописывается в технологии контроля (операционной технологической карте акустико-эмиссионного контроля сварного вертикального цилиндрического резервуара). В практике АЭ-контроля могут применяться следующие системы классификации источников АЭ:
- по амплитудному критерию;
- по интегральному критерию;
- по локально-динамическому критерию;
- по интегрально-динамическому критерию (в соответствии с японским стандартом NDIS 2412-80);
- по критериям кода ASME (Американское общество инженеров-механиков);
- по критериям, предусмотренным в технологии MONPAC (с использованием параметров «силовой индекс» и «исторический индекс», которые определяются по специальным выражениям в зависимости от удвоенной площади по огибающей импульса акустической эмиссии на осциллограмме);
- по критерию непрерывной АЭ. Фиксация непрерывных сигналов акустической эмиссии, превышающих заданный порог, может указывать на наличие течи, сквозных трещин в контролируемом резервуаре, протечек в уплотнениях и так далее. Дискретная (она же – импульсная) акустическая эмиссия говорит о страгивании и скачкообразном продвижении трещины, либо о разрушении включений, либо о коррозии под напряжением и пр.
Местоположение источников АЭ определяется по отдельным участкам поверхности (при организации зонного контроля) либо точнее (при использовании многоканальной локации). В последнем случае погрешность определения координат источника АЭ не превышает удвоенную толщину стенки либо 5% от расстояния между преобразователями акустической эмиссии. Программное обеспечение современных комплексов для акустико-эмиссионного контроля могут отображать карту локации источников АЭ непосредственно на карте градуировки (схема-развёртка и указанием положения ПАЭ) контролируемого вертикального стального резервуара. Такая визуализация упрощает выделение зон повышенной концентрации индикаций акустической эмиссии (кластеров), их сопоставление с технологической топологией резервуара, идентификацию механических шумов и иных ложных сигналов, не обусловленных развитием дефектов.
Все события акустической эмиссии (единичное действие источника АЭ) записываются в режиме реального времени. После этого выделяются параметры сигналов акустической эмиссии для последующего накопления и анализа. Время поступления и длительность сигналов акустической эмиссии измеряется с разрешением не более 1 мкс. При этом время начала импульса определяется моментом времени достижения импульсом заданного порога. Чем больше длительность переднего фронта импульса и чем меньше его амплитуда, тем больше может быть погрешность измерения времени. На искажение принимаемой акустической волны влияет и дисперсия – зависимость скорость распространения колебаний от частоты. Если акустико-эмиссионный контроль сварного вертикального цилиндрического резервуара продолжается больше четырёх часов, то его могут разделять на этапы, с раздельной оценкой источников АЭ на каждом из них.
Что касается шумов и помех, то под первыми подразумеваются непрерывные сигналы, которые не связаны с наличием дефектов в контролируемом объекте и которые мешают обнаружению сигналов акустической эмиссии и определению их параметров. Помехами же называют импульсные сигналы акустического или электромагнитного происхождения, также не связанные с наличием дефектов в контролируемом объекте. Минимальный уровень шумов определяют собственные тепловые шумы преобразователя акустической эмиссии и коэффициент шума входных каскадов усилителя либо предусилителя (при наличии). Собственные шумы аппаратуры (Uша) для акустико-эмиссионного контроля РВС не должны превышать 10 мкВ (в исключительных случаях, при наличии научно-технического обоснования – до 20 мкВ), а уровень непрерывных акустических либо электромагнитных шумов (Uш) должен быть ниже порогового напряжения (Uпор) не менее чем на 6 дБ (Uш < Uпор = Uша + 6 дБ). В противном случае предпринимают меры для снижения уровня шумов, а если это не помогает, то проведение акустико-эмиссионного контроля приостанавливают. Электромагнитные помехи, как правило, имеют малую длительность и большую амплитуду. Связанные с трением шумы, напротив, отличаются малой амплитудой и большой длительностью – больше, чем у сигналов АЭ от трещины. Эти и другие признаки помогают выделять из шумов полезные сигналы. Что касается импульсных шумов и помех, то ограничения по ним определяют в зависимости от условий выполнения АЭ-контроля и стремятся к тому, чтобы средняя частота их регистрации не превышала 0,01 Гц. Впрочем, существуют технологии акустико-эмиссионного контроля, построенные на принципе беспороговой регистрации данных. Шумы, наряду с полезными сигналами, фиксируются преобразователями АЭ, проходят через предварительный, затем – через широкополосный усилитель. Далее, уже посредством ПО, данные подвергаются математической обработке (с использованием метода главных компонент, быстрого преобразования Фурье, метода адаптивной фильтрации и так далее). Регистрация и статическая обработка таких массивов данных требует больших вычислительных мощностей, но помогает лучше учитывать особенности условий АЭ-контроля и источников АЭ для выделения полезных сигналов и выявления зарождающихся дефектов.
По завершении акустико-эмиссионного контроля выполняется проверка работоспособности аппаратуры и преобразователей, проверяется коэффициент предварительного усиления, коэффициент основного усиления и уровень порога по каналам. Все эти данные могут отражаться в протоколе акустико-эмиссионного контроля.
Оформление результатов АЭ-контроля
По результатам акустико-эмиссионного контроля сварных вертикальных цилиндрических резервуаров специалисты II и III уровня составляют протоколы, заключения, отчёты. Перечень и форма предоставления отчётных документов согласуются с предприятием-заказчиком. В отчёте приводятся сведения:
- о проконтролированном резервуаре (допускается составлять единый отчёт по нескольким однотипным РВС);
- о руководящих методических и нормативных технических документах, в соответствии с которым проводился акустико-эмиссионный контроль;
- об условиях контроля (температуры окружающей среды, металла и испытательной жидкости или газа, уровень акустических шумов и электромагнитных помех);
- об акустических свойствах металла;
- о количестве и схеме расстановки преобразователей акустической эмиссии;
- о системе классификации источников АЭ;
- об используемой аппаратуре для акустико-эмиссионного контроля и её параметрах (количество каналов, коэффициенты усиления для разных групп ПАЭ и акустических каналов, собственные шумы, дата поверки и/или калибровки и прочее);
- о проведении контроля и графике нагружения;
- о зарегистрированных источниках АЭ, включая схему-развёртку (карту градуировки) резервуара с обозначением ПАЭ, источников АЭ и основных конструкционных элементов (сварные соединения, патрубки, рёбра жёсткости и прочее). В отчёте приводятся данные по всем зафиксированным источникам АЭ с указанием класса, координат и с оценкой степени опасности по выбранной системе классификации;
- о лаборатории НК и персонале, который был задействован для акустико-эмиссионного контроля резервуара вертикального стального. В частности, приводится наименование ЛНК, номер, дата выдачи и срок действия свидетельства об аттестации. Помимо ФИО специалистов АЭ, указываются номера, даты выдачи и сроки действия их квалификационных удостоверений (аттестации), квалификационные уровни и прочее.
Результаты неразрушающего контроля дополнительно фиксируются в соответствующем журнале, который ведётся в лабораториях по каждому виду (методу) НК. В соответствии с Федеральными нормами и правилами по неразрушающему контролю на ОПО, утверждёнными Приказом Ростехнадзора от 1 декабря 2020 года №478, оформление и хранение результатов НК допускается не только на бумажных носителях, но и в электронном виде, с использованием усиленной квалифицированной электронной подписи (п. 13). Но это ещё зависит от согласования с заказчиком работ по АЭ-контролю. В самой ЛНК результаты акустико-эмиссионного контроля РВС хранятся не менее 5 лет либо не менее срока, установленного документами, на основании которых назначены либо изменены сроки службы (остаточный ресурс) объекта контроля. Старые правила ПБ 03-593-03 требовали, чтобы результаты АЭ-контроля хранились не менее 10 лет либо до повторного АЭ-контроля.
Где купить аппаратуру для АЭ-контроля или найти специалистов для его проведения на РВС
Одним из спонсоров проекта «Дефектоскопист.ру» является ведущий разработчик технологий и аппаратуры для акустико-эмиссионного контроля. Также с нами сотрудничают уважаемые учебные центры, где можно пройти обучение на дефектоскописта АЭ даже «с нуля».
НПО «Алькор». Научно-производственное объединение было основано в 1991 году и находится в Дзержинске. НПО «Алькор» занимается серийным производством аппаратуры для акустико-эмиссионного контроля, разработкой индивидуальных технологий контроля и методических рекомендаций, проведением НК на ОПО и пр. Система менеджмента качества сертифицирована по международному стандарту ISO 9001. Собственная система лабораторий неразрушающего контроля аттестована по правилам СДАНК-01-2020 в ЕС ОС и выполняет работы по акустико-эмиссионному контролю на РВС по всей стране. В том числе – на объектах ПАО «Транснефть», «СИБУР», «Роснефть», «ЛУКОЙЛ», «Сургутнефтегаз» и др. НПО «Алькор» самостоятельно выпускает комплексы интегрального мониторинга «Ресурс-2000», мобильные диагностические комплексы «Эксперт-2014», портативные диагностические комплексы «Эксперт-2020», преобразователи акустической эмиссии, разные вспомогательные комплектующие, разрабатывает ПО и т.д. Гарантийную и послегарантийную техническую поддержку осуществляет собственный сервисный центр в Нижегородской области. Чтобы подобрать решения для акустико-эмиссионного контроля сварных вертикальных цилиндрических резервуаров или заказать выполнение работ по АЭ-контролю под ключ, обращайтесь в НПО «Алькор»: +7 (8313) 25-26-10, +7 (920) 074-13-23, alcor@alcor.pro.
НУЦ «Качество». Научно-учебный центр создан в Москве в 2005 году. Независимый орган по аттестации персонала и лабораторий неразрушающего контроля в Единой системе оценки соответствия в области промышленной безопасности, экологической безопасности, безопасности в энергетике и строительстве (по правилам СДАНК-01-2020 и СДАНК-02-2020). Также НУЦ «Качество» – лицензированная образовательная организация, уполномоченный орган по аккредитации испытательных лабораторий в соответствии с ISO/IEC 17025:2005 и орган по сертификации персонала в Национальной системе аккредитации. Полный перечень услуг НУЦ «Качество» по подтверждению компетентности персонала и лабораторий НК доступен на форуме. Узнать подробнее о подготовке специалистов акустико-эмиссионного контроля в НУЦ «Качество»: +7 (495) 777-41-02, +7 (495) 744-70-52, info@centr-kachestvo.ru.
Региональный центр аттестации, контроля и диагностики (РЦАКД). Структурное подразделение Инженерной школы неразрушающего контроля и безопасности ФГАУ ВО «Национальный исследовательский Томский политехнический университет». ТПУ был создан на базе знаменитого НИИ Интроскопии. В РЦАКД можно пройти обучение методу акустической эмиссии с последующей аттестацией по правилам СДАНК-02-2020. Здесь же можно пройти аттестацию лабораторию по правилам СДАНК-01-2020. Экзаменационные центры РЦАКД работают в Магнитогорске, Новокузнецке, Излучинске, Великом Новгороде и Санкт-Петербурге. Выпускники ТПУ и РЦАКД трудятся на предприятиях «Газпрома», «Транснефти», «ЛУКОЙЛ», «СИБУР» и др. Более подробная информация о подготовке специалистов по акустико-эмиссионному контролю резервуаров вертикальных стальных и других ОПО: +7 (3822) 41-79-22, +7 (3822) 41-99-21, ndt@tpu.ru.
Многие из партнёров «Дефектоскопист.ру» предоставляют форумчанам хорошие скидки. Берегите бюджет своей лаборатории – и покупайте оборудование неразрушающего контроля только у надёжных поставщиков!