В продолжение
дискуссии, которая пару недель назад (как быстро летит время!) случилась в нашем
"Телеграме". Небольшой эксперимент.
Цель: проверить, будет ли в режиме А-скан наблюдаться эхо-сигнал от границы раздела покрытие-металл, и посмотреть, как он будет себя вести на разных образцах и с разными настройками толщиномера.
Матчасть: ультразвуковой толщиномер "Булат 3", преобразователь П112-5-10/2-Е, образец-ступенька из стали толщиной 1,0-15,0 мм, настроечный образец толщиной 20 мм, меры толщины покрытия толщиной 0,484 мм и 1,96 мм, контактный гель "КЛЕВЕР УЗК-Про".
Порядок выполнения:
1. Наносим гель на ступеньку толщиной 1,0 мм, сверху прижимаем меру толщины покрытия (0,484 мм) и наносим гель на неё тоже. Методом
Зонд-Эхо выполняем измерения. Видим, что измерения происходит по второму отражению (2,2 мм). Заметим, что скорость в мере толщины покрытия 2 650 мм/с, то есть примерно в 2 раза меньше, чем скорость в стали. Видимо, поэтому в сумме это даёт результат вдвое больше толщины основания.
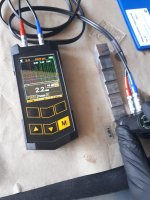
2. Кстати, если попытаться просто сдвинуть правее зону контроля, чтобы исключить первый сигнал, то это ничего не изменит.
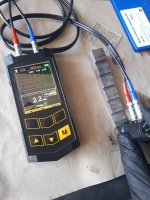
3. Первый сигнал - вероятно, от границы раздела, что легко проверить, подняв усиление на 4 дБ и доведя отрицательную полуволну до порога срабатывания (1,2 мм).
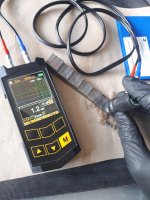
4. После переключения на метод
Зонд-Эхо-Покрытие результат уже больше похож на правду. Первый сигнал, выделенный жёлтым маркером, это таки сигнал от границы раздела, а "второй" сигнал, выделенный красным маркером - первый донный.
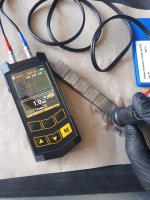
И в режиме
Цифры всё тоже гуд.
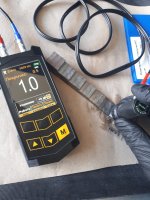
5. На всякий случай пробуем проделать то же самое на
настроечном образце толщиной 20 мм. Опять видим два эхо-сигнала. Левее - от границы раздела покрытие-металл, правее - донный. Простой сдвиг границы зоны контроля не помогает - но при использовании метода
Зонд-Эхо-Покрытие результаты получаются корректные.
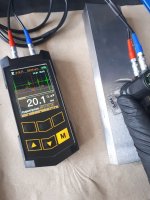
6. Напоследок возвращаемся к ступеньке, на толщину 1,0 мм, но берём меру толщины покрытия потолще, 1,96 мм. Заметим, что амплитуда эхо-сигнала от границы раздела получается ещё больше, даже без повышения усиления.
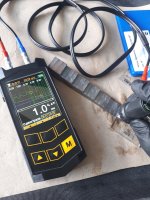
Выводы: эхо-сигнал от границы раздела покрытие-металл таки наблюдается (что я и пытался доказать в том обсуждении), но его амплитуда зависит от толщины покрытия, толщины основания, усиления, адгезии и прочих условий (что тоже было понятно изначально). Кстати, по поводу адгезии. Между покрытием и основанием я наносил контактный гель. С одной стороны, читерство (получилось обойтись меньшим усилением), с другой - это ведь всего лишь эксперимент, ради которого намертво склеивать образцы было бы нерационально.
И да: для нормальных измерений толщины стенки под покрытием и/или толщины покрытий сам по себе А-скан не панацея. Нужна возможность не только "увидеть" отражение от границы раздела, но и как-то работать с этим сигналом, отталкиваться от него. Нужна либо пара стробов (пример мы
показывали ранее), либо, как в "Булат 3", такой прикольный метод, как
Зонд-Эхо-Покрытие.