Визуальный и измерительный контроль стыковых сварных соединений промысловых и магистральных трубопроводов
Визуальный и измерительный контроль (ВИК) стыковых кольцевых сварных соединений повсеместно проводится при строительстве, ремонте и реконструкции промысловых и магистральных трубопроводов. Это основополагающий вид неразрушающего контроля (НК), с которого начинается экспертиза промышленной безопасности, техническое диагностирование и ревизия эксплуатируемых газопроводов, трубопроводов нефти и нефтепродуктов – объектов, подведомственных Федеральной службе по экологическому, технологическому и атомному надзору (Ростехнадзор). Цель визуального и измерительного контроля – проверить геометрию сварного шва, выявить имеющиеся поверхностные дефекты, измерить их линейные размеры и оценить стык по нормам отбраковки. Последние приводятся в нормативно-технической документации (НТД) и зависят от категории объекта, типа сварного соединения, уровня качества, диаметра, толщины стенки, способа сварки, зоны прокладки и пр. Визуальному и измерительному контролю подлежит сварной шов и околошовная зона (ОШЗ), или зона термического влияния (ЗТВ), протяжённость которой опять-таки определяется положениями НТД и операционной технологической карты (ОТК, примеры – здесь). К проведению НК другими методами стык допускается только после удовлетворительных результатов ВИК. Выявленные дефекты подлежат устранению с повторным ВИК – и только тогда можно переходить к радиографическому, ультразвуковому, магнитопорошковому и капиллярному контролю. Долгие годы главным руководящим документом по ВИК была «Инструкция по визуальному и измерительному контролю» РД 03-606-03, которая прекратила действие с 1 января 2021 года, но которая остаётся важным справочным источником. По состоянию на апрель 2024 года основным документом по визуальному и измерительному контролю на опасных производственных объектах (ОПО) является Руководство по безопасности "Методические рекомендации о порядке проведения визуального и измерительного контроля", утверждённое Приказом Ростехнадзора от 16 января 2024 года №8, и ГОСТ Р ИСО 17637-2014 «Контроль неразрушающий. Визуальный контроль соединений, выполненных сваркой плавлением». Также один из трендов последних лет – внедрение технологий автоматизированного визуального и измерительного контроля (АВИК), которые уже широко практикуются на объектах «Транснефти» (см. РД-25.160.10-КТН-016-15 «Магистральный и трубопроводный транспорт нефти и нефтепродуктов. Неразрушающий контроль сварных соединений при строительстве и ремонте магистральных трубопроводов») и «Газпрома» (см. СТО Газпром 15-1.3-004-2023 «Сварка и неразрушающий контроль сварных соединений. Неразрушающие методы контроля качества сварных соединений промысловых и магистральных трубопроводов»).Содержание:
Основные процедуры визуального и измерительного контроля сварных соединенийВыявляемые дефекты
Средства ВИК
Требования к лабораториям НК
Требования к специалистам ВИК
Автоматизированный ВИК
Куда обратиться за аттестацией
Где выгоднее покупать инструменты для ВИК
Далее по тексту речь идёт преимущественно о визуальном и измерительном контроле выполненных сварных соединений, хотя многие НТД могут предусматривать послойный ВИК в процессе сварки. Делается это для того, чтобы заблаговременно обнаружить недопустимые поверхностные дефекты (свищи, прожоги, включения, поры, раковины, трещины и прочее) и исправить их до выполнения следующего валика или слоя шва. Если он подлежит термообработке, то ВИК проводится как до, так и после её выполнения. Для температур -30 градусов Цельсия и ниже руководящие НТД также могут требовать проведения ВИК кольцевых стыковых сварных соединений дважды: сразу после окончания сварки и затем после полного остывания стыка.
Порядок проведения визуального и измерительного контроля стыковых сварных соединений трубопроводов
«Классический» (ручной, не автоматизированный) ВИК состоит из нескольких ключевых этапов.- Наружный осмотр стыка с целью оценки его контролепригодности. Важно убедиться, что к сварному соединению обеспечен беспрепятственный и безопасный двухсторонний доступ, как минимум, к лицевой поверхности объекта. Расстояние от грунта до трубопровода должно составлять не менее 0,4–5 м. У дефектоскописта должна быть возможность осматривать сварной шов и ОШЗ с расстояния до 600 мм, причём никакие препятствия не должны мешать тому, чтобы делать это под разными углами (оптимальным для осмотра считаются углы ≥30 градусов к плоскости стыка). Для фокусировки глаза на объекте расстояние до него желательно выдерживать не менее 250 мм. Освещённость контролируемой поверхности должна составлять не менее 500 лк и проверяется при помощи люксметра с действующей поверкой (см. ниже). Шероховатость поверхности должна быть не хуже Ra=12,5 мкм (Rz=80 мкм). Её можно проверить по аттестованным образцам шероховатости, изготовленным по ГОСТ 9378-93 «Образцы шероховатости поверхности (сравнения). Общие технические условия», либо при помощи профилометров или профилографов. На практике сразу могут оценивать шероховатость поверхности сварного соединения для последующего капиллярного (или магнитопорошкового), ультразвукового, радиографического контроля и пр. Для них требуется Ra=6,3 мкм (Rz=40 мкм), а то и Ra=3,2 мкм (Rz=20 мкм). Перед проведением визуального и измерительного контроля поверхность сварного соединения должна быть также зачищена от масляных пятен, изоляции, загрязнений, брызг металла, окалины, ржавчины, краски. Если речь идёт о подземных трубопроводах – то перед проведением визуального и измерительного контроля также обеспечивают безопасный спуск в траншею (например, по временной деревянной лестнице), а её откосы должны быть сделаны таким образом, чтобы не допустить обрушения грунта. Для наземных трубопроводов – обеспечивают участок проведения работ лестницами, козлами, строительными лесами и пр. Если контролепригодность и контроледоступность стыка не удовлетворяют требованиям, отражённым в техкарте и НТД, то работы по ВИК приостанавливают до устранения нарушений. В условиях трассы это решается взаимодействием со «смежными» подрядчиками – производителями сварочно-монтажных работ и/или заказчиком. Если (когда) условия для работы созданы – можно переходить к п. 2.
- Разметка. При наличии мерительного пояса разметка на трубопроводе сводится лишь к обозначению начала отсчёта координат, который принято вести по часовой стрелке относительно направления потока рабочей (транспортируемой) среды. Точка отсчёта может быть привязана, например, к клейму сварщика или другому месту. Главное требование – однозначность определения начала отсчёта координат для всех методов НК. Поскольку визуальный и измерительный контроль – первый, но не единственный метод неразрушающего контроля, которому подвергают сварные соединения газопроводов и нефтепроводов, то важно обеспечить единый подход к разметке. В старых НТД, например, можно встретить рекомендацию о разметке сварного соединения на участки по 300–500 мм, в соответствии с размером рентгеновской плёнки для последующего радиографического контроля. При наличии мерительного пояса это не актуально – главное, чтобы «0» на нём совпадал с одной и той же точкой начала отсчёта координат. На трубопроводах её часто наносят несмываемым маркером по металлу. Тот же мерительный пояс может использоваться для последующего ПВК (МПД), УЗК, РК. Более современное решение для разметки и последующей обработки результатов ВИК – измерительный комплекс фотофиксации PhotoPlate от научно-производственного центра «Кропус», особенно удобный на трубопроводах. Комплекс состоит из магнитной измерительной ленты с QR-кодами. Дефектоскописту нужно закрепить её на трубе и последовательно сфотографировать все участки (фотоаппарат входит в комплект). Далее – необходимо загрузить снимки в специальное программное обеспечение (ПО) на персональном компьютере (ПК). ПО автоматически «выпрямляет» снимки и расставляет их в правильной последовательности. Изображение кольцевого сварного соединения формируется в идеальную плоскую полосу высокого разрешения. Тем самым устраняется погрешность, обусловленная искажением снимков из-за цилиндрической поверхности трубы. Благодаря этому, используя ресурсы ПО, оператор может с точностью до 0,1 мм измерять размеры дефектов, масштабировать изображение, наносить маркеры, добавлять примечания и пр. Готовые снимки и результаты ВИК хранятся в электронном виде на ПК либо облачном сервисе сколь угодно долгое время. Что же касается мерительных поясов, то они могут изготавливаться под конкретный диаметр трубопровода из ПВХ либо прорезиненного капрона. Главные требования к материалу – прочность, сохранение эластичности даже на морозе, влагостойкость, устойчивая к изнашиванию маркировка, удобные и надёжные крепления. Чаще всего это «липучки», «пряжки» либо магниты. Мерительный пояс состоит из двух прошитых слоёв, внутри которых находятся свинцовые маркировочные знаки, изображения которых видны на рентгенограммах. Для ВИК важно то, что «0» на внешней стороне пояса может отсутствовать – например, шкала может начинаться с 1 дм и далее идти с шагом 1 см. Подробнее об этом нюансе мы рассказывали на нашем YouTube-канале.
- Визуальный контроль. Проводится с использованием просмотровой и/или измерительной лупы с подсветкой и без (чаще всего требуется диапазон увеличения от 3 до 7 крат), фонарика (при необходимости). Но главное – это, безусловно, глаза дефектоскописта, его зоркость, внимательность, сосредоточенность, опыт. Визуальный контроль по природе своей – органолептический, то есть выполняется, прежде всего, органами чувств, хоть и с допустимым применением просмотровой лупы. Определение шероховатости по образцам, кстати, тоже считается органолептическим. Цель визуального контроля – выявление поверхностных дефектов: пор, усадочных раковин (кратеров), трещин, прожогов, свищей, шлаковых включений, неполностью заполненных кромок, подрезов, неаккуратной поверхности шва (грубой чешуйчатости, неравномерной ширины шва), случайного оплавления основного металла, отслоений. При наличии доступа к обратной стороне шва также фиксируют имеющиеся провисы (местное превышение проплава), вогнутость обратной стороны шва, непровары и пр. Важной характеристикой считается минимальное угловое разрешение двух точек на контролируемой поверхности – у «среднестатистического» человеческого глаза она составляет порядка 1 дуговой минуты. То есть на расстоянии 300 мм разрешение может достигать 0,09 мм, а на расстоянии 600 мм – до 0,18 мм. Выявленные дефекты обводят маркером и/или фиксируют на эскизе сварного соединения, с указанием типа дефекта и координат. Их также отражают в схеме сварного соединения, которая должна прилагаться к заключению по результатам ВИК.
- Измерительный контроль. Цель – измерить линейные размеры и/или площадь поверхностных дефектов, выявленных на этапе визуального контроля, а также проверить соответствие геометрических параметров готового сварного шва нормативным требованиям. Данный этап проводится уже с помощью аттестованных средств измерений (СИ) с действующей поверкой (если они внесены в Государственный реестр СИ РФ) или калибровкой (если не внесены). К таковым инструментам относятся: шаблоны сварщика, металлические измерительные линейки, рулетки, измерительные лупы, штангенциркули и др. Если визуальный и измерительный контроль проводится на этапе сборки под сварку, то могут пригодиться также щупы, с помощью которых проверяют зазор между кромками. СИ должны проходить поверку (калибровку) раз в год. В заключении по результатам визуального и измерительного контроля сварных соединений трубопровода приводятся данные о серийном номере каждого СИ, свидетельствах о поверке, сертификатах о калибровке и сроках их действия. В зависимости от требований НТД и типа дефектов при проведении ВИК измеряют максимальный размер, максимальную ширину, длину вдоль шва, длину поперёк шва, глубину, суммарную протяжённость. Измерениям также подлежит смещение кромок и параметры сварного шва: выпуклость (высота усиления), вогнутость, выпуклость и вогнутость корня, ширина, профиль шва, чешуйчатость, межваликовые западания. Некоторые дефекты недопустимы любых размеров – например, трещины, кратеры, прожоги, непровары, неполностью заполненные кромки. У других есть некие допуски. К таковым относятся, например, подрезы, поры, шлаковые и вольфрамовые включения, неаккуратная поверхность шва и т.д.
- Оформление заключения. Цель – обработать данные, собранные в процессе визуального и измерительного контроля и сформулировать вывод о соответствии или несоответствии сварного соединения трубопровода требованиям НТД. Многие НТД требуют относить стык к категории «Годен», «Ремонт» или «Вырезать». Заключение оформляется по шаблону, приведённому в руководящем документе и/или договоре на выполнение работ по НК. В заключении по результатам визуального и измерительного контроля, как правило, указывают наименование трубопровода и номер участка (километраж), заказчика, подрядчика и лабораторию НК (включая номер и срок действия свидетельства об аттестации). Также в заключении указывается ФИО и квалификационный уровень дефектоскописта, дата проведения контроля, руководящий нормативно-технический документ и номер (шифр) операционной технологической карты. Перечисляются задействованные СИ, приводятся номера свидетельств о поверке и/или сертификатов калибровки с указанием срока их действия и пр. Сюжет о подготовке заключения по результатам ВИК сварного шва доступен на YouTube-канале «Дефектоскопист.ру».
Типы дефектов, выявляемых для визуального и измерительного контроля сварных соединений
Очень условно, но ВИК стыкового сварочного шва направлен на решение трёх главных задач.- Выявление дефектов, недопустимых вне зависимости от размеров и суммарной протяжённости на длине оценочного участка шва. То есть это в любом случае «непроходящие» дефекты. В случае со стыковыми сварными соединениями к таковым относятся кратеры (усадочные раковины), трещины (кратерные, радиальные, разветвлённые, продольные, поперечные – вообще любые), прожоги, неполное заполнение кромок, случайное оплавление основного металла в результате зажигания или гашения дуги, наплывы и пр. Такие дефекты можно увидеть невооружённым глазом либо с помощью просмотровой или измерительной лупы.
- Выявление дефектов, которые могут оказаться допустимыми, и измерение их размеров. К этой условной второй группе дефектов относятся непровары, подрезы, поры, инородные металлические и неметаллические включения (шлаковые, флюсовые, вольфрамовые). Если их размеры (длина вдоль шва и поперёк шва, диаметр, высота или глубина) не превышают допустимых значений, то сварное соединение даже может быть признано годным. Какие дефекты и при каких условиях считаются допустимыми – должно определяться руководящими нормативными документами и отражается в операционной технологической карте ВИК. Ещё один важный фактор – суммарная протяжённость на оценочном участке шва, длина которого тоже определяется в руководящей НТД. На практике длина оценочного участка может составлять, например, 1/6 периметра сварного шва, либо равняться его периметру (для труб диаметром меньше 100 мм), либо составлять 300 мм (для труб диаметром ≥100 мм) и т.д. То есть каждый отдельный дефект может быть допустим, но если их слишком много и их суммарная протяжённость не вписывается в допуск – то это уже брак. Другой важный нюанс – присутствие других дефектов на том же участке шва, на котором оцениваются те или иные дефекты. Так, согласно вышеупомянутому стандарту СТО Газпром 15-1.3-004-2023 (таблица 6.2), на участках сварного шва со смещением больше 2,0 мм не допускаются любые подрезы, а на участках максимально допустимого смещения недопустимы вообще любые дефекты.
- Проверка геометрических параметров сварного соединения. К таковым относится смещение кромок, перелом осей (угловое смещение), ширина шва, выпуклость (усиление, высота усиления шва), профиль шва (плавность перехода), чешуйчатость, межваликовые западания (для многопроходных швов) и др. Конкретный перечень геометрических параметров, подлежащих измерению при проведении ВИК, приводится в руководящих нормативных технических документах и операционных технологических картах. Там же должны содержаться указания по порядку выполнения таких замеров: сколько их нужно сделать, в каких точках (плоскостях), на каком расстоянии друг от друга, с применением каких СИ и т.д. Так, если в каких-то местах чешуйчатость и межваликовые западания превышают допустимые значения, то это считается неравномерной поверхностью шва (грубой чешуйчатостью). Другой пример – неравномерная ширина шва, то есть её чрезмерное колебание по периметру стыка и отклонение от нормированных значений. В заключении по результатам визуального и измерительного контроля приводятся сведения обо всех местах, где геометрические параметры сварного соединения не соответствуют допускам, с указанием конкретных фактических значений и координат относительно точки начала отсчёта (на схеме проконтролированного стыка).
Средства визуального и измерительного контроля сварных швов
Для разметки удобнее использовать мерительные пояса. По состоянию на июнь 2023 года на некоторых объектах разрешено использовать электронную разметку (например, для автоматизированного ВИК с использованием сканеров).Средства для ВИК обычно поставляются в наборах. Они могут комплектоваться под разные отрасли, разные условия применения. Для неразрушающего контроля на опасных производственных объектах, подведомственных Ростехнадзору, используются наборы для ВИК с поверкой либо калибровкой. В их составе присутствуют инструменты, прошедшие метрологическую аттестацию (процедуру оценки соответствия), утверждённые в качестве средств измерений и внесённые в Государственный реестр СИ РФ.
Для визуального и измерительного контроля стыковых сварных соединений трубопроводов чаще всего используются следующие средства контроля.
- Линейка измерительная. Чаще всего для ВИК применяются металлические линейки длиной 300 мм, хотя, например, для измерения перелома осей на трубопроводах большого диаметра в зависимости от требований НТД могут понадобиться линейки длиной 1000 мм и больше. Кроме того, линейка может пригодиться для измерения длины дефектов вдоль и поперёк шва и расстояния между ними.
- Штангенциркуль. В наборах для визуального и измерительного контроля сварных соединений широко применяются штангенциркули типа ШЦ-1-125 и ШЦ-1-150 со значением отсчёта по нониусу 0,05 мм, глубиномером и губками для измерения внутренних и внешних размеров, расположенными с двух сторон. Это один из самых универсальных инструментов, с помощью которого можно измерять ширину и высоту шва, выпуклость и вогнутость обратной стороны шва, глубину подрезов. Даже чешуйчатость и глубину западаний между валиками многопроходного шва разрешается измерять при помощи штангенциркуля. Погрешность измерения всего ±0,1 мм позволяет использовать его для измерений в диапазоне даже до 0,5 мм. Некоторые модификации (например, ШЦ-1-150 марки «ЭЛИТЕСТ») и вовсе имеют погрешность всего ±0,05 мм. Есть на рынке и цифровые штангенциркули, с дискретностью отсчётного устройства 0,01 мм и предельно допускаемой абсолютной погрешностью при измерении внешних размеров в пределах ±0,02–0,03 мм. Некоторые из них даже внесены в Государственный реестр СИ РФ. Пример – ШЦЦ-1-150-0,01 SHAN.
- Рулетка измерительная. Ещё один инструмент, который относится к так называемым штриховым мерам длины. При проведении визуального и измерительного контроля стыковых сварных соединений трубопроводов может пригодиться для измерения наружного диаметра и овальности соединяемых деталей. Полученные результаты измерения пересчитываются по формулам, которые есть, например, в РД 03-606-03 и в Руководстве по безопасности "Методические рекомендации о порядке проведения визуального и измерительного контроля", утверждённом Приказом Ростехнадзора от 16 января 2024 года №8. Кроме того, рулетка может оказаться более удобным решением для измерения максимального размера поверхностных дефектов, особенно большой протяжённости и особенно на трубопроводах малого диаметра, к которым очень затруднительно вплотную прижимать металлическую линейку.
- Измерительная лупа. Предназначена для измерения размеров поверхностных дефектов: диаметра, длины вдоль шва, длины поперёк шва, максимального размера, максимальной ширины, расстояния между одиночными дефектами и пр. Измерительные лупы отличаются от обычных просмотровых наличием шкалы линейных измерений длиной до 30 мм (по 15 мм в обе стороны от нуля). Цена деления шкалы – 0,1 мм. Дополнительно к ней могут быть предусмотрены и другие вспомогательные шкалы. Пример – измерительная лупа ЛИ-3-10x LED «ЭЛИТЕСТ» с линейной, угловой (от 0 до 90 градусов) и радиусной (от 0 до 10 мм) шкалой, а также кругами и квадратами разных размеров. Такая разметка помогает дефектоскописту быстрее и точнее измерять размеры одиночных несплошностей. Измерительные лупы также могут иметь подсветку и диапазон увеличения изображения до 10 крат. У обычных просмотровых луп, для сравнения, увеличение обычно не превышает 8 крат. Измерительные лупы помогают дефектоскописту более пристально рассматривать дефекты сварных соединений и тем самым делают визуальный и измерительный контроль более информативным и достоверным.
- Шаблоны сварщика. Самый массовый из них, конечно же, УШС-3. Ввиду сравнительно большой погрешности (±0,5 мм) он не совсем подходит для измерения глубины подрезов и пор в диапазоне менее 2,5 мм, однако именно УШС-3 поставляется в большинстве наборов для ВИК, представленных на рынке. Правда, компания «АРИОН» (группа компаний «РЕНТЕСТ», Нижний Новгород) изготавливает модификации шаблона сварщика УШС-3Т и УШС-4Т с погрешностью линейных измерений в пределах ±0,1 мм. Они внесены в Госреестр СИ РФ, поставляются с поверкой, удовлетворяют всем требованиям упомянутого выше регламента РД-25.160.10-КТН-016-15 и успешно применяются на объектах «Транснефти», «Газпрома» и др. Помимо УШС-3 и его модификаций, для визуального и измерительного контроля стыковых сварных соединений трубопроводов широко применяются и другие шаблоны сварщика – УШС-1 (он же УШК-1, или шаблон Красовского), TapiRUS, WG1, WG2+, Bridge Cam, шаблон Красовского, Ушерова-Маршака и др. Для оценки профиля шва удобно пользоваться шаблоном плавности перехода «ЭЛИТЕСТ», который представляет собой металлическую линейку с метрической шкалой и рабочей гранью под углом 120˚.
- Приспособление для измерения глубины подрезов и смещения кромок. В основе таких приборов используется индикатор часового типа, утверждённый в качестве СИ, поэтому поставляются они с паспортом и свидетельством о поверке/калибровке. Пример приспособления для измерения глубины подрезов и смещения кромок – ПСК-10М «ЭЛИТЕСТ», о котором есть обучающий сюжет на YouTube-канале «Дефектоскопист.ру». В основе устройства – индикатор часового типа с внешней круговой (цена деления – 0,01 мм) и внутренней (цена деления – 1,0 мм) шкалой. Погрешность измерений не превышает ±0,01 мм (10 мкм). Для сравнения: у шаблона сварщика УШС-3, повторимся, она достигает 0,5 мм. Индикатор часового типа фиксируется в опорном кронштейне из алюминия. У модификации ПСК-10М в основание кронштейна встроен магнит для надёжного удержания на изогнутой поверхности трубопровода. В комплекте поставки ПСК-10М предусмотрено 2 измерительных наконечника. Плоский измерительный наконечник предназначается для измерения выпуклости (высоты усиления) сварного шва и выпуклости с обратной стороны шва (местного превышения проплава). Острый наконечник – для измерения глубины подрезов и иных поверхностных дефектов, смещения кромок, чешуйчатости и западаний между валиками. Для подготовки ПСК-10М нужно закрепить измерительный наконечник на подвижной части индикатора часового типа, а сам ИЧТ зафиксировать в державке опорного кронштейна при помощи стопорного устройства. Далее необходимо установить прибор на плоскую поверхность объекта контроля и произвести его калибровку – выставить его на «0». Диапазон измерений ПСК-10 по паспорту – от 0 до 10 мм (хотя фактически ход стрелки на внутренней круговой шкале от 0 до 11 мм, что нужно для корректной работы прибора). В процессе калибровки этот диапазон можно «распределить» для измерений над рабочей поверхностью и под ней. Так, в процессе калибровки можно установить «0» таким образом, что измерения глубины поверхностных несплошностей и, например, смещения кромок будут выполняться в диапазоне от «0» до «-5» мм, а измерение выпуклости сварного шва – от «0» до «+5» мм. При желании диапазон измерений можно «распределить» и в других «пропорциях», не обязательно «поровну». Например, можно откалибровать прибор таким образом, чтобы измерения выполнялись над рабочей поверхностью в пределах от «0» до «7», а под ней – от «0» до «-3» мм и т.д. Главное – корректно откалибровать обе круговые шкалы, внутреннюю и наружную. Опорный кронштейн при этом должен быть устойчив на поверхности объекта контроля, без перекосов и «заваливаний». Более подробно порядок работы с приспособлением для измерения глубины подрезов и смещения кромок ПСК-10 изложен здесь. А вот здесь – показан процесс проведения визуального и измерительного контроля кольцевого стыкового сварного соединения, в том числе – с данным прибором.
- Люксметр. Прибор для измерения освещённости контролируемой поверхности – важной процедуры на этапе подготовки к проведению ВИК. Измерители освещённости являются средствами измерений – соответственно, подлежат утверждению типа и внесению в Государственный реестр СИ РФ. Для визуального и измерительного контроля сварных соединений на ОПО можно применять люксметры с действующей поверкой (калибровкой). Сведения об этом должны быть отражены в заключении по результатам ВИК. Сам люксметр представляет собой компактный прибор с выносным измерительным зондом либо моноблок со встроенным светочувствительным датчиком. Независимо от варианта исполнения корпуса ключевой элемент – измерительная головка с полупроводниковым кремниевым фотодиодом и светофильтрами для обеспечения спектральной чувствительности для той или иной длины волны. На рынке также есть люксметры, которые сочетают в себе функции яркомера и/или термогигрометра. В первом случае дополнительно к освещённости они могут измерять яркость светового потока. Во втором – позволяют ещё и определять относительную влажность и температуру воздуха. В реальной практике визуального и измерительного контроля сварных соединений газопроводов и нефтепроводов до проверки освещённости при помощи люксметра доходит далеко не всегда. ВИК проводится под открытым небом, в дневное время – поэтому зачастую это, скорее, формальность. Но если руководящие НТД и/или утверждённые заказчиком формы исполнительной документации требуют указывать фактическую освещённость при выполнении ВИК, то без рабочего и поверенного люксметра на объекте уже точно не обойтись.
- Образцы шероховатости сравнения (ОШС). Позволяют органолептическим методом оценивать шероховатость поверхности трубопровода путём сравнения с плоским либо выпуклым образцом – визуально и на ощупь (опробыванием пальцами рук). ОШС поставляются наборами, в которых предусмотрены образцы с разной шероховатостью от Ra 0,4 мкм до Ra 25 мкм или от Rz 10 мкм до Rz 320 мкм. Сами ОШС изготавливаются из плоских либо цилиндрических заготовок с использованием разных технологий обработки – точения, фрезерования, строгания, шлифования, развёртывания, протягивания, полирования и пр. Образцы шероховатости поверхности могут быть изготовлены из стали, меди, алюминия, латуни, чугуна или иных сплавов. ОШС должны соответствовать упомянутому выше ГОСТ 9378-93 и подлежат метрологической аттестации. Поверка таких образцов регламентируется методикой МИ 1850-88. Для применения ОШС при проведении визуального и измерительного контроля сварных соединений на ОПО важно убедиться, что к образцам прилагается паспорт и действующее свидетельство о поверке (если ОШС внесены в Госреестр СИ, и во ФГИС «Аршин» такие действительно есть) либо сертификат о калибровке (если не внесены – и такие встречаются чаще всего). Сведения о данных документах, как правило, нужно приводить в заключении по результатам ВИК.
- Профилометр. Более продвинутая альтернатива образцам шероховатости поверхности и органолептическому методу её оценки. Контактные и бесконтактные (лазерные и оптические), профилометры могут измерять среднее арифметическое отклонение профиля в пределах базовой длины (Ra), высоту неровностей профиля по 10 точкам (Rz), среднеквадратичное отклонение профиля (Rq) и другие величины в зависимости от подключаемого датчика. Наиболее продвинутые профилометры поддерживают беспроводную передачу данных по Wi-Fi, имеют энергонезависимую память результатов замеров и оснащаются высокоскоростными процессорами для быстрой обработки данных. Есть модели со встроенными датчиками. И конечно, для применения на ОПО предпочтение стоит отдавать профилометрам, внесённым в Государственный реестр СИ РФ.
К набору для визуального и измерительного контроля прилагается комплект документов: паспорта, свидетельства о поверке и/или сертификат калибровки – причем как на отдельные СИ, так и на весь набор в целом.
Для автоматизированного визуального и измерительного контроля (АВИК) также может потребоваться инфракрасный пирометр или контактный термометр. Это нужно для того, чтобы оператор мог замерять температуру поверхности трубопровода и воздуха и следить за тем, чтобы они соответствовали диапазону рабочих температур комплекса АВИК.
Также в наборы для ВИК могут входить и другие полезные принадлежности, которые не являются средствами измерений. К таковым, например, относятся просмотровые лупы, фонарики, маркеры по металлу, инспекционные зеркала для осмотра обратной стороны (корня, обратного валика) сварного шва и т.д. Наборы плоских щупов используются на этапе сборки под сварку для определения зазора между кромками свариваемых деталей. Для визуального и измерительного контроля чаще всего используется №4 со щупами толщиной 0,1–10,0 мм.
Требования к лабораториям для выполнения ВИК сварных соединений
Для работы на опасных производственных объектах, подведомственных Ростехнадзору, лаборатории должны пройти аттестацию, как того требуют Федеральные нормы и правила в области промышленной безопасности «Основные требования к проведению неразрушающего контроля технических устройств, зданий и сооружений на опасных производственных объектах» (приказ Ростехнадзора от 01.12.2020 года №478). По состоянию на июнь 2023 года в РФ функционирует две основные системы неразрушающего контроля:- Единая система оценки соответствия в области промышленной безопасности, экологической безопасности, безопасности в энергетике и строительстве (ЕС ОС). Координирующий орган – НТЦ «Промышленная безопасность». Правила аттестации ЛНК в ЕС ОС – СДАНК-01-2020.
- Система неразрушающего контроля на опасных производственных объектах Российского общества по неразрушающему контролю (СНК ОПО РОНКТД). Центральный орган – СРО «Ассоциация «Национальное агентство контроля сварки». Правила аттестации изложены в СНК ОПО РОНКТД-03-2021.
Помимо этого, лаборатории неразрушающего контроля и испытательные лаборатории могут пройти аккредитацию в Национальной системе аккредитации. Это может быть добровольное решение либо обязательная процедура – в случаях, предусмотренных Федеральным законом от 28.12.2023 года №412-ФЗ. Например, если испытательная лаборатория занимается оценкой соответствия продукции техническим регламентам Таможенного союза с выдачей соответствующих сертификатов. К такой продукции могут относиться соединительные детали трубопроводов, запорно-регулирующая арматура и пр. Аккредитация в Росаккредитации проводится в соответствии со стандартом ГОСТ ISO/IEC 17025-2019 «Общие требования к компетентности испытательных и калибровочных лабораторий». Схема аккредитации – процедура достаточно сложная, не дешёвая и легко может растянуться на полгода-год. Лаборатория должна подтвердить высокую производственную культуру во всех аспектах, от профессиональной подготовки персонала и учёта оборудования до составления технологических карт, ведения журналов, развития системы менеджмента качества и пр. Поэтому аккредитация считается едва ли не самым трудоёмким, но вместе с тем – наиболее авторитетным способом подтверждения компетентности лабораторий неразрушающего контроля и испытательных лабораторий.
Пройти аккредитацию ЛНК также могут в упомянутой выше ЕС ОС. НТЦ «Промышленная безопасность» осуществляет данную деятельность согласно ГОСТ ISO/IEC 17011-2018 «Оценка соответствия. Требования к органам по аккредитации, аккредитующим органы по оценке соответствия». Испытательные лаборатории подтверждают соответствие требованиям СДА-15-2009. Непосредственно их оценкой занимаются территориальные уполномоченные органы в разных регионах РФ.
Для работы на объектах «Транснефти» ЛНК должна пройти аккредитацию в соответствии с ОР-26.160.40-КТН-064-15.
Визуальный и измерительный контроль – лишь один из видов и методов неразрушающего контроля, которые лаборатории заявляют в своей области аттестации. Обычно таких видов (методов) НК, сильно больше: самая популярная комбинация для работы на трубопроводах – ВИК, УК, РК, ПВК, МК.
Отдельные требования предъявляются к руководителям (начлабам). Они должны пройти отдельную аттестацию в соответствии с Федеральными нормами и правилами «Правила промышленной безопасности при использовании оборудования, работающего под избыточным давлением» (приказ Ростехнадзора от 15.12.2020 года №536) для соответствующих классов ОПО, предусмотренных Федеральным законом от 21.07.1997 года №116-ФЗ «О промышленной безопасности опасных производственных объектов». Начальниками лабораторий неразрушающего контроля часто становятся специалисты с опытом работы в НК. В ряде отраслей минимально допустимый стаж для таких руководителей составляет 3 года.
Лаборатория неразрушающего контроля должна располагать собственным архивом нормативно-технических документов, соответствующих области аттестации. К таковым относятся международные, национальные, отраслевые стандарты, методики и технологические инструкции. Также в ЛНК составляют операционные технологические карты под конкретные объекты контроля, например, типовые сварные соединения трубопроводов определённого диаметра, категории и уровня качества. Разработкой техкарт могут заниматься специалисты II и III уровня. На практике технологические карты утверждаются начальником (руководителем) ЛНК, хотя этот нюанс в НТД раскрыт не полностью. Есть мнение, что техкарты и вовсе не обязательно утверждать специалистами III уровня – многие руководящие документы этого не требуют. Правила СНК ОПО РОНКТД-02-2021 допускают согласование технологических карт и даже технологических инструкций специалистами 2-го уровня (п. 4.3). К слову, в некоторых отраслях (например, по стандартам Российского речного регистра и Российского морского регистра) правом такого утверждения обладают только специалисты III уровня. В действительности это ещё во многом зависит от пожеланий заказчика и регулируется договорными обязательствами.
Используемые для визуального и измерительного контроля инструменты подлежат внесению в паспорт лаборатории и в реестр оборудования НК. По каждому набору для ВИК и другим средствам НК заводят учётную карточку (учётный лист) с указанием его наименования, производителя, серийного и инвентарного номера, даты изготовления и ввода в эксплуатацию, сведений о поверке/калибровке и пр. Сопроводительные документы по всем средствам для ВИК (паспорта, инструкции, свидетельства, сертификаты) тоже должны храниться в лаборатории. Также в ЛНК обязаны вести графики поверки и калибровки, а также аттестации (например, образцов шероховатости поверхности), проверки технического состояния и технического обслуживания средств НК. Ответственность за учёт, хранение, метрологическое обеспечение возлагают на конкретных сотрудников лаборатории. В настоящее время в российских ЛНК успешно применяется специализированное программное обеспечение для управления складом оборудования. Пример – сервис LAB365.
Требования к дефектоскопистам ВИК
Визуальный и измерительный контроль сварных соединений промысловых и магистральных трубопроводов выполняют аттестованные дефектоскописты и специалисты неразрушающего контроля. Как и в случае с лабораториями, чаще всего аттестацию персонала НК для работы на таких объектах проходят в двух системах.- ЕС ОС. Руководящий документ – СДАНК-02-2020 «Правила аттестации персонала в области неразрушающего контроля».
- СНК ОПО РОНКТД. Руководящий документ – СНК ОПО РОНКТД-02-2021 «Аттестация специалистов неразрушающего контроля».
- I уровень. Проходить аттестацию на него мало смысла – разве что в целях сокращения минимального стажа для последующей аттестации на II уровень. Но фактически с I уровнем можно лишь проводить работы по визуальному и измерительному контролю, но без права выдачи заключения о годности/негодности сварных соединений. То же самое могут делать ученики и помощники дефектоскопистов, пока набирают производственный стаж для аттестации на II уровень. Многие специалисты неразрушающего контроля именно так и приходят в профессию: устраиваются в ЛНК и первое время трудятся без квалификационного удостоверения под началом более опытного наставника, зарабатывая опыт, знания и навыки.
- II уровень. Согласно правилам СДАНК-02-2020 (п. 3.7), для аттестации дефектоскописта ВИК на II уровень в Единой системе оценки соответствия производственный стаж должен составлять минимум 3 месяца. По правилам СНК ОПО РОНКТД-02-2021 (приложение Е), минимальный производственный стаж для получения того же 2-го квалификационного уровня зависит от уровня профессионального образования кандидата и наличия у него 1-го уровня. В одних случаях стаж должен составлять 6 месяцах, а в других – аттестоваться на 2-й уровень можно и вовсе без производственного опыта.
- III уровень. Самый высокий: даёт позволяет делать то же, что и II уровень, только ещё даёт дополнительные права. В том числе – разрабатывать и подтверждать методики и инструкции по неразрушающему контролю (а не только перерабатывать их к конкретным рабочим условиям). Срок действия аттестации на III уровень составляет 5 лет, а не 3 года, как у I и II уровня.
Также с 2021 года, дополнительно к ЕС ОС, НТЦ «Промышленная безопасность» создал Систему добровольной сертификации в области неразрушающего контроля, в которой дефектоскописты тоже могут подтвердить свою квалификацию.
В «Транснефти» действует своя система: для работы на её объектах специалисты НК должны пройти аттестацию в соответствии с ОР-03.120.00-КТН-139-18.
Помимо наличия квалификационного удостоверения, к дефектоскопистам предъявляются и другие требования. Так, персонал НК должен проходить предварительный (при трудоустройстве в лабораторию) и периодические медицинские осмотры (приказ Минздрава РФ от 28.01.2021 года №29н). Особое внимание уделяется проверке зрения. С 2021 года в России даже действует посвящённый этому ГОСТ Р ИСО 18490-2020 «Контроль неразрушающий. Оценка остроты зрения специалистов неразрушающего контроля». Подробнее о требованиях к состоянию зрения дефектоскопистов мы рассказывали здесь.
Независимые органы по аттестации персонала НК (Аттестационные центры по аттестации специалистов НК) проводят предаттестационную подготовку, профессиональное обучение и повышение квалификации дефектоскопистов визуального и измерительного контроля по разным программам продолжительностью, как правило, от 16 до 80 академических часов. Но чаще всего учебные программы рассчитаны на 40 часов теоретических и практических занятий. В процессе обучения технологии ВИК внимание уделяется самым разным аспектам.
- Физические основы визуального и измерительного метода неразрушающего контроля сварных соединений. В отличие от того же ультразвукового контроля, метод ВИК специфичен тем, что в физических основах очень много сведений, которые как будто лишь опосредованно относятся к реальной практике. Так, в учебных программах по ВИК большое внимание уделяется свету – его распространению, поляризации, стробоскопическому эффекту основы, явлениям дисперсии, преломления, отражения света, флуоресценции, световым величинам, светотехническим свойства материалов и т.д. Также к теоретическим основам ВИК относят сведения о строении глаз, зрительной функции, зрительном восприятии, процессах аккомодации, адаптации к разной освещённости и пр. Изучение «физики» визуального и измерительного метода неразрушающего контроля включает в себя также знакомство с основами оптики, принципами действия луп, зеркал, очков, телескопических систем, эндоскопов, микроскопов, средств дистанционного визуального контроля и фотофиксации результатов ВИК. Всё это сложновато постоянно держать в голове – поэтому вскоре после сдачи экзаменов многие из этих знаний забываются даже практикующими дефектоскопистами. И по этой причине неотъемлемым этапом первичной и повторной аттестации остаётся предаттестационная подготовка, когда в течение нескольких дней специалист может спокойно погрузиться в теорию и подготовиться к общей части квалификационного экзамена.
- Основы металловедения. Для проведения визуального и измерительного контроля сварных соединений неплохо бы иметь представление о строении и свойствах чёрных и цветных металлов и их сплавов. Знать о диаграмме «железно-углерод», видах термообработки, фазовых превращениях, процессах сварки плавлением и/или пластическим деформированием, «строении» прилегающей ко шву зоны термического влияния и свойствах входящих в неё разных участков. Будущие дефектоскописты ВИК изучают типовые поверхностные дефекты, вероятные отклонения от заданных геометрических параметров сварных соединений и причины их возникновения.
- Измерение линейных и угловых величин. Для визуального и измерительного контроля сварных соединений трубопроводов широко применяются всевозможные штриховые меры длины – рулетки и рулетки. Некоторые НТД в других отраслях, кстати, допускают измерять размеры (максимальный размер и ширину, диаметр) поверхностных дефектов при помощи трафаретов и плёночных шаблонов, предназначенных для расшифровки рентгенограмм при проведении радиографического контроля. Для ВИК сварных соединений газопроводов и нефтепроводов также важно научиться работать со штангенциркулем, корректно считывать показания нониуса и пользоваться глубиномером. В том числе – измерять ширину швов, максимальный размер и максимальную ширину выходящих на поверхность дефектов, высоту шва (выпуклость, усиление), выпуклость и вогнутость обратной стороны шва, глубину подрезов, западаний между валиками и пр. Для измерения перелома осей (углового смещения) свариваемых элементов цилиндрической формы (труб), их наружного диаметра и овальности – понадобится также навык работы с линейкой, рулеткой и знание специальных формул. Причём НТД может предусматривать измерение перелома осей на базе 1000 мм или даже 5000 мм, так что может понадобиться навык работы с линейками длиной 1000 мм или даже со складным метром. Но чаще всего эти параметры всё же контролируют на этапе сборки под сварку. Для измерения углов (например, при контроле тавровых или угловых сварных соединений) учатся работе с угольниками, катетомерами, угломерами, шаблонами сварщика. Возвращаясь к стыковым сварным соединениям, отметим также, что для визуального и измерительного контроля важно понимать специфику измерения высоты шва, выпуклости обратной стороны и вогнутости при смещении кромок и соединении разнотолщинных элементов. Так, выпуклость и вогнутость стыкового сварного шва измеряют по максимальной высоте или глубине соответственно относительно поверхности шва от уровня расположения наружной поверхности деталей. Если речь идёт о разнотолщинных деталях, то выпуклость и вогнутость поверхности сварного шва оценивают относительно линии, соединяющей края шва в одном сечении. Ну а если соединяемые детали имеют один и тот же диаметр и номинальную толщину, то выпуклость и вогнутость шва измеряют относительно уровня поверхности детали, расположенной выше. Также специалисту ВИК неплохо бы иметь представление о допустимой погрешности измерений. В зависимости от руководящего НТД она может отличаться, но чаще всего в документах воспроизводятся допуски из таблицы №1 упомянутой выше инструкции РД 03-606-03, которая по состоянию на июнь 2023 года применяется лишь как справочный источник. Аналогично - допустимые погрешности приведены в Руководстве по безопасности "Методические рекомендации о порядке проведения визуального и измерительного контроля", утверждённом Приказом Ростехнадзора от 16 января 2024 года №8.
- Применение различных шаблонов сварщика. Шаблонов много, их модификаций – ещё больше, поэтому в помощь дефектоскопистам ВИК группа компаний «РЕНТЕСТ» выпустила специальное учебное пособие. В нём приведены наиболее распространённые в РФ шаблоны, выпускаемые под брендом «ЭЛИТЕСТ», но не только. По каждому из них – перечислены геометрические параметры сварных соединений и линейные размеры поверхностных дефектов, которые можно измерять с помощью того или иного шаблона. И, конечно же, приведены методические рекомендации по выполнению измерений при проведении ВИК сварочных швов. При всей универсальности и простоте штангенциркуля – зачастую для измерения геометрических параметров сварных швов гораздо удобнее и быстрее пользоваться шаблонами. К тому же штангенциркуль не предназначен для измерения смещения кромок, зато многие шаблоны сварщика это позволяют. При работе с шаблонами сварщика и другими измерительными инструментами важно понимать, в каких именно местах и каким образом нужно выполнить измерения. Такие места должны быть указаны в конкретных НТД и чертежах. Выпуклость (усиление) и ширину шва, например, в зависимости от методики нужно измерять не реже чем через 1 м по длине сварного соединения, причём не менее, чем в 3-х сечениях, равномерно распределённых по окружности (п. 8.1.12 в РД-25.160.10-КТН-016-15). Аналогичный подход – к измерению смещения кромок. Но первоочередным, конечно же, является измерительный контроль на «сомнительных» участках, где есть подозрение на несоответствие геометрических параметров стыка требованиям НТД по результатам визуального контроля.
- Нормативные технические документы. Дефектоскопист должен хорошо знать стандарты, методики, технологические инструкции и операционные технологические карты, по которым он проводит ВИК. Сегодня при строительстве и ремонте промысловых и магистральных трубопроводов применяется огромное количество способов и режимов сварки. Поэтому требования к геометрическим параметрам сварных соединений и, соответственно, нормы отбраковки по результатам визуального и измерительного контроля, могут сильно отличаться. Это также зависит от категории трубопровода, диаметра, толщины стенки, уровня качества, разделки кромок и пр. Поэтому специалисту ВИК нужно чётко знать, по какому именно документу выполняются работы и какие нормы оценки качества заложены для контролируемого сварного соединения. Не менее важную роль играет правильное оформление результатов визуального и измерительного контроля, грамотное описание всех выявленных дефектов сварного соединения, указание их координат, корректное отображение на схеме стыка. Типовые формы заключений обычно приведены в руководящих НТД. В договоре с заказчиком могут быть указаны дополнительные индивидуальные требования к оформлению результатов ВИК.
- Правила безопасности. Дефектоскописту лучше не пренебрегать средствами индивидуальной защиты (перчатки, очки, каска). Летом – можно могут спасать накидки с антимоскитной сеткой. Дополнительно к экзамену на знание правил безопасности непосредственно в лаборатории дефектоскопист проходит обязательный инструктаж по технике безопасности под роспись в соответствующем журнале.
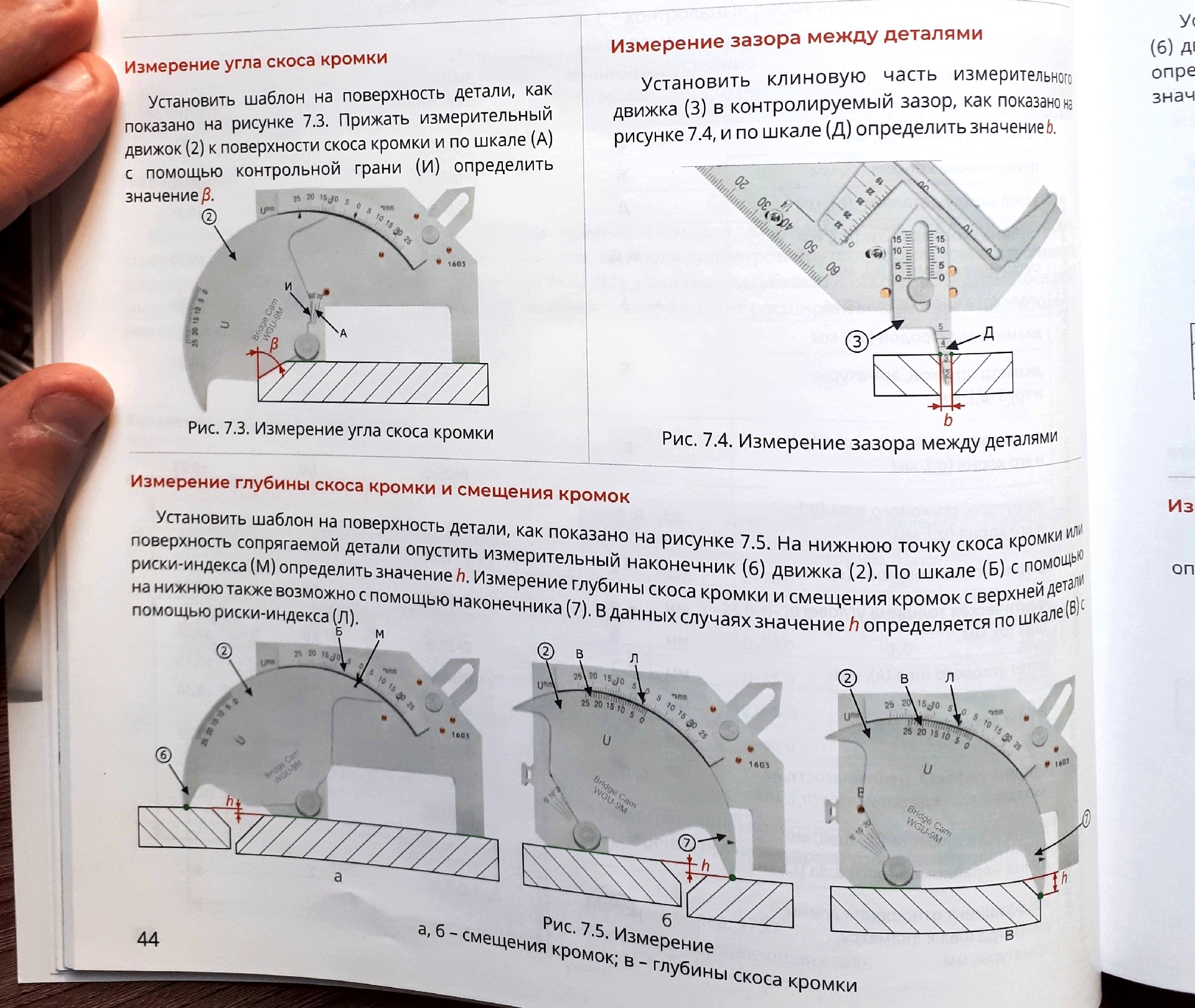
Как мы отметили выше, визуальный и измерительный контроль – первый, но далеко не единственный метод неразрушающего контроля сварных соединений, который практикуется на промысловых и магистральных газопроводах и нефтепроводах. Поэтому на таких объектах работают дефектоскописты, которые обучены и аттестованы не только по ВИК, но и по другим методам НК – УК, РК, ПВК, МК т.д. Чаще всего такие специалисты трудятся вахтами, по 1–2, реже – по 3 и более месяца. Дополнительная трудность – полевые условия, особенно при строительстве новых трубопроводов, если на трассе ещё толком не создана инфраструктура и не решены вопросы с обустройством дорог, бани, душа, кухни. Когда жить приходится в вагон-городках и работать то при экстремально низких, то при изнуряюще высоких температурах. Летом к этому прибавляется гнус, риск встретиться с дикими животными, отсутствие нормального сообщения с «большой землёй» из-за болотистой местности. Зимой – холод, сугробы и пр. Кроме того, работа на «линейке» – это часто цейтнот, жёсткие сроки, необходимость соответствовать темпу движения сварочной колонны.
Поэтому от дефектоскопистов, которые в полевых условиях проводят визуальный и измерительный контроль сварных соединений трубопроводов, требуется недюжинная выдержка, выносливость, стрессоустойчивость, бережное отношение к своему здоровью, физическому и психологическому.
Автоматизированный ВИК
Проводится с применением специальных сканеров («АВИКСкан», «ВИЗИО»), которые автоматически перемещаются по периметру сварного соединения, выполняют лазерное сканирование его поверхности (сварного шва и околошовной зоны, или оценочного участка основного металла) и записывают данные для последующей обработки при помощи специализированного программного обеспечения. Современные комплексы для АВИК поддерживают беспроводную передачу данных по Wi-Fi на ПК (ноутбук) оператора. Сканеры для автоматизированного визуального и измерительного контроля определяют геометрические параметры сварных соединений и оценивают их по нормам оценки качества в соответствии с заданными настройками и руководящими нормативными техническими документами. Сканирование выполняется непрерывно, с шагом 1 мм, так что изображение получается очень детализированным. Наиболее продвинутые системы умеют «строить» 3D-модель сварного шва, которую оператор может рассматривать с разными ракурсами, задействуя ресурсы специализированного ПО. Программа при этом может выделять разными цветами выявленные поверхностные дефекты разных типов и участки шва, геометрические параметры которых не удовлетворяют допускам. На выходе получается подробный иллюстрированный отчёт по типовой форме в соответствии с выбранным НТД, с перечислением поверхностных дефектов и отклонений геометрических параметров стыков, их координат, линейных размеров, с классификацией, а также с заключением о годности/негодности шва.Сами комплексы для автоматизированного визуального и измерительного контроля представляют собой модуль с лазерным триангуляционным 2D-сканером, фото- и видеокамерой. Модуль перемещается по направляющему поясу (бандажу), который устанавливают на сварном соединении трубопровода. За передвижение комплекса отвечает каретка с электроприводом и автономным питанием от аккумуляторов. Скорость может достигать 1,5 м в минуту. Для корректной работы лазерных датчиков в конструкции предусматривают специальные шторки, которые защищают их от бликов и позволяют выполнять сканирование даже при ярком солнечном свете. Комплексы АВИК адаптированы к тяжёлым полевым условиям: сканеры «ВИЗИО МТ», например, имеют степень защиты IP67 и рассчитаны на работу при температурах от -40 до +40 ˚С. При этом модули взаимозаменяемые – их можно приобретать отдельно от каретки, бандажа, ПК и пр.
Строго говоря, АВИК очень сильно отличается от обычного, «традиционного» ВИК, поскольку выполняется с использованием лазерных сканеров, а не органолептически. На практике встречаются системы, интегрированные с модулями для проведения автоматизированного ультразвукового или радиографического контроля. По состоянию на июнь 2023 года технологии автоматизированного визуального и измерительного контроля сварных соединений всё активнее внедряются в лабораториях, которые выполняют работы по НК на трубопроводах. Пример – новые стандарты «Газпрома», в которых уделяется большое внимание применению комплексов АВИК. Они должны пройти аккредитацию в Национальной системе аккредитации и пройти процедуру утверждения типа средств измерений (должны быть внесены в Госреестр СИ РФ). Стандарты «Газпрома» также требуют, чтобы методика проведения АВИК прошла оценку соответствия технологии (аттестации). Специалисты, которые занимаются проведением автоматизированного ВИК, должны пройти обучение у производителя или в уполномоченном учебном центре с выдачей подтверждающего документа.
Где аттестовать лабораторию и персонал НК для проведения ВИК на ОПО
Среди спонсоров форума «Дефектоскопист.ру» есть сразу несколько авторитетных организаций в данной области.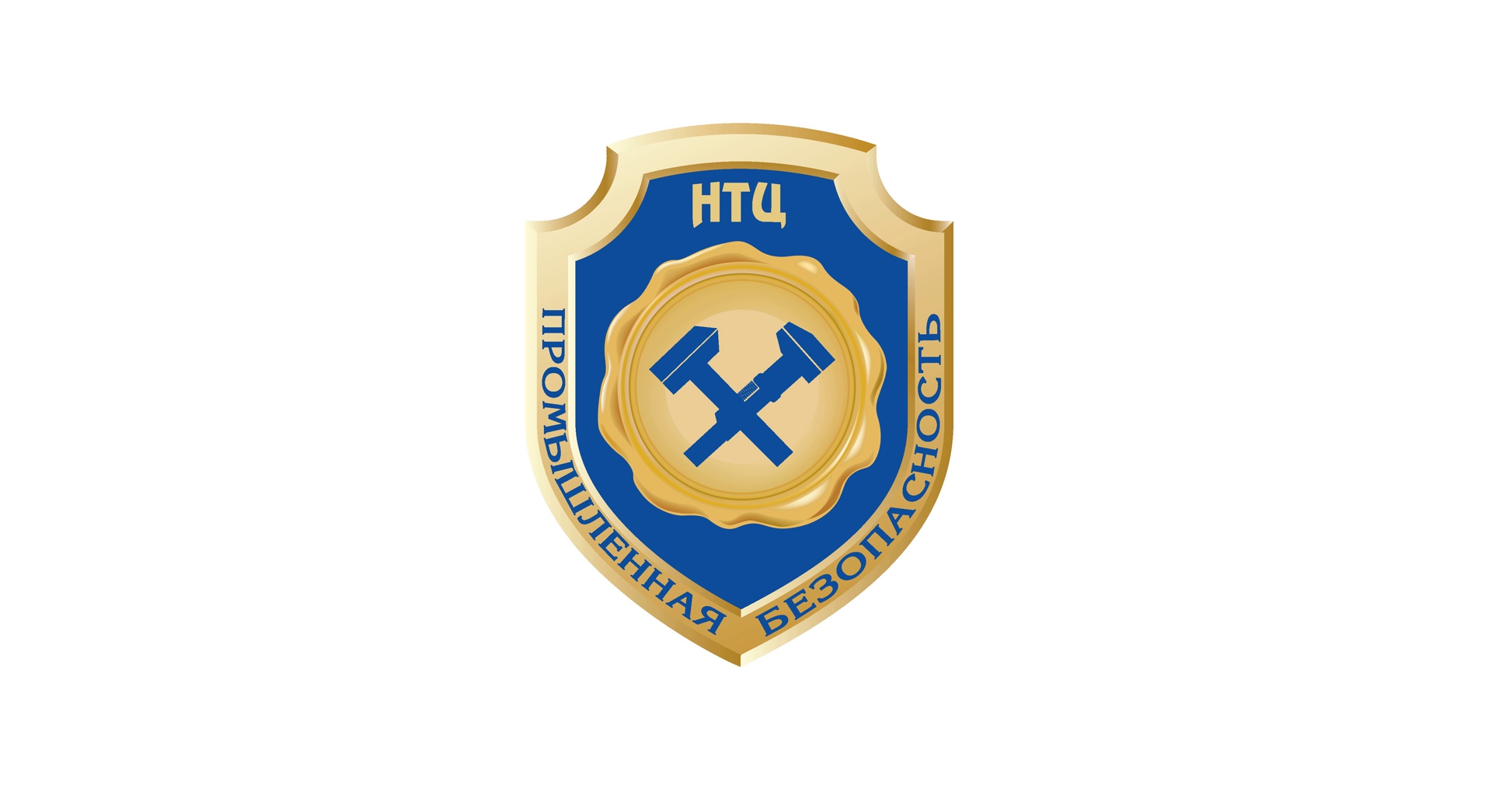
- НТЦ «Промышленная безопасность». Научно-технический центр с более чем 30-летней историей. Координирующий орган упомянутой выше Единой системы оценки соответствия в области промышленной безопасности, экологической безопасности, безопасности в энергетике и строительстве. По состоянию на июнь 2023 года в структуре ЕС ОС функционирует 36 Независимых органов по аттестации персонала НК и 38 Независимых органов по аттестации лабораторий НК в разных регионах России. В 2022 году в ЕС ОС было аттестовано 2 013 ЛНК и 35 293 дефектоскопистов. НТЦ «Промышленная безопасность» – действующий член международных организаций IAF, ILAC и APAC. Контакты центра: +7 (495) 500-51-98, +7 (495) 287-92-20, ntc@oaontc.ru.
- НУЦ «Качество». Научно-учебный центр в Москве с региональными экзаменационными центрами по всей РФ. Основан в 2005 году. Независимый орган по аттестации персонала и Независимый орган по аттестации лабораторий неразрушающего контроля в ЕС ОС, лицензированная образовательная организация и орган по сертификации продукции в Системе добровольной сертификации «ИНТЕРГАЗСЕРТ». Полный перечень направлений деятельности и разрешительных документов НУЦ «Качество» приведён здесь. Программы обучения дефектоскопистов визуальному и измерительному контролю сварных соединений рассчитаны на 40 академических часов и составлены в соответствии с ISO 9712:2012 и международным стандартом ISO/TS 25107.2:2019. Узнать стоимость и сроки аттестации ЛНК и/или сертификации персонала НК: +7 (495) 777-41-02, +7 (495) 744-70-52, info@centr-kachestvo.ru.
- РЦАКД. Региональный центр аттестации, контроля и диагностики – подразделение Инженерной школы неразрушающего контроля и безопасности (ИШНКБ) ФГАОУ ВО «Национальный исследовательский Томский политехнический университет». Также является НОАП и НОАЛ в ЕС ОС и проводит аттестацию персонала и лабораторий НК по правилам СДАНК-01-2020 и СДАНК-02-2020. Экзаменационные центры РЦАКД функционируют в Санкт-Петербурге, Великом Новгороде, Магнитогорске, Новокузнецке, Излучинске (ХМАО). Одно из ключевых преимуществ РЦАКД – сильный кадровый состав. Здесь трудятся четыре доктора технических наук, семь кандидатов технических наук и девятнадцать специалистов НК III уровня. О подготовке дефектоскопистов ВИК мы рассказывали в этом тексте. Узнать стоимость обучения и аттестации персонала НК, а также аттестации лаборатории можно по телефонам +7 (3822) 41-77-29 и +7 (3822) 41-99-21, а также по почте ndt@tpu.ru.
Где купить средства визуального и измерительного контроля сварных соединений трубопроводов
В числе спонсоров проекта «Дефектоскопист.ру» есть несколько надёжных разработчиков и поставщиков средств ВИК.«Рентгенсервис». Предприятие группы компаний «РЕНТЕСТ» в Нижнем Новгороде. С 1998 года занимается поставкой и производством средств неразрушающего контроля вообще и визуального и измерительного контроля сварных соединений в частности. Входящая в группу «РЕНТЕСТ» компания «АРИОН» изготавливает множество оборудования, инструментов и принадлежностей для ВИК под брендом «ЭЛИТЕСТ». В том числе: приспособление для измерения глубины подрезов и смещения кромок ПСК-10 (подробно о работе с ним мы рассказывали здесь), шаблоны сварщика (более 30 модификаций, от УШС-3 и WG1 до Bridge Cam и WG12), мерительные пояса «СПРУТ», угольники, штангенциркули, измерительные рулетки, измерительные лупы с подсветкой и без, телескопические инспекционные зеркала и пр. Многие разработки утверждены в качестве средств измерений и внесены в Государственный реестр СИ РФ – к примеру, те же шаблоны сварщика УШС-3 и УШС-4. Единый отдел продаж: +7 (800) 302-67-32, xrs@xrs.ru.
ЕЦНК (Единый Центр Неразрушающего Контроля). Основа в 2010 году. Центральный офис находится в Санкт-Петербурге, есть представительства в Москве, Казани, Самаре, Уфе и Екатеринбурге. Компания представляет широкий перечень услуг на рынке неразрушающего контроля, работая по принципу «единого окна». В ЕЦНК можно решить практически любую задачу, включая аттестацию ЛНК, обучение и аттестацию персонала, закупку оборудования, принадлежностей и дефектоскопических материалов, поверку и калибровку СИ, ремонт аппаратуры и пр. Для визуального и измерительного контроля сварных соединений ЕЦНК выпускает наборы «Эксперт №1» с поверкой и «Эксперт №2» с калибровкой (о комплекте мы рассказывали здесь). Справочная служба ЕЦНК: +7 (800) 777-18-43, ecnk@ecnk.ru.
ГЕО-НДТ. Компания с большим складом в Москве и более чем 13-летним опытом поставок оборудования для лабораторий неразрушающего контроля и испытательных лабораторий. Выпускает собственную серию наборов «ВИК-НДТ» для визуального и измерительного контроля сварных соединений. Комплекты поставляются в мягких сумках и ударопрочных кейсах. «ВИК-НДТ» внесён в Государственный реестр СИ РФ и поставляется со свидетельством о поверке или калибровки. Заказать набор для ВИК можно по телефону +7 (495) 988-79-77 и по почте info@geo-ndt.ru.
NDT Club. Совместно с НПФ «АКА-Скан» компания NDT Club разработала комплект «ТрассоВИК», созданный специально для визуального и измерительного контроля сварных соединений при строительстве и ремонте промысловых и магистральных газопроводов и нефтепродуктов. Главная его особенность – вместительная шаровидная сумка с тросом для более удобного и безопасного перекидывания через траншею. Заказы на «ТрассоВИК» принимаются по телефону +7 (800) 600-57-06 и почте info@ndt-club.com.
НИИИН МНПО «СПЕКТР». Для визуального и измерительного контроля сварных соединений институт с 2019 года выпускает шаблон TapiRUS, внесённый в Государственный реестр СИ РФ (№82433-21) и защищённый патентом Федеральной службы по интеллектуальной собственности. У шаблона TapiRUS – рекордное количество измеряемых параметров при проведении ВИК по сравнению с любыми другими отечественными и импортными шаблонами сварщика. TapiRUS позволяет измерять свыше 20 геометрических характеристик заготовленных и собранных под сварку деталей, а также готовых стыковых и угловых сварных швов и поверхностных дефектов. Погрешность измерений линейных размеров не превышает 0,1 мм. Это позволяет успешно применять TapiRUS на объектах «Транснефти», «Газпрома», атомнадзора и на других объектах, подведомственных Ростехнадзору. Для более комфортной и производительной работы с шаблоном TapiRUS было разработано мобильное приложение для устройств на ОС Android. «TapiRUS_ассистент» позволяет быстро и точно определять расчётные значения геометрических параметров сварных соединений и критерии оценки качества по конкретным нормативным техническим документам. Приложение «TapiRUS_ассистент» внесено в Единый реестр российских программ для ЭВМ и баз данных. Помимо «классической» версии TapiRUS, у шаблона есть Smart-версия с цифровыми индикаторами, голосовым помощником, автоматической обработкой результатов ВИК и онлайн-оформлением заключений. Заказать «обычную» или Smart-версию TapiRUS для визуального и измерительного контроля сварных соединений по современным стандартам: +7 (495) 323-50-28, sales@niiin.ru.
Многие из партнёров «Дефектоскопист.ру» предоставляют форумчанам хорошие скидки. Берегите бюджет своей лаборатории – и покупайте оборудование неразрушающего контроля только у надёжных поставщиков!